Think Again: Major automation companies tout next-generation tools offering digitalization advantages, mobility and flexibility, for greater speed to higher profits.
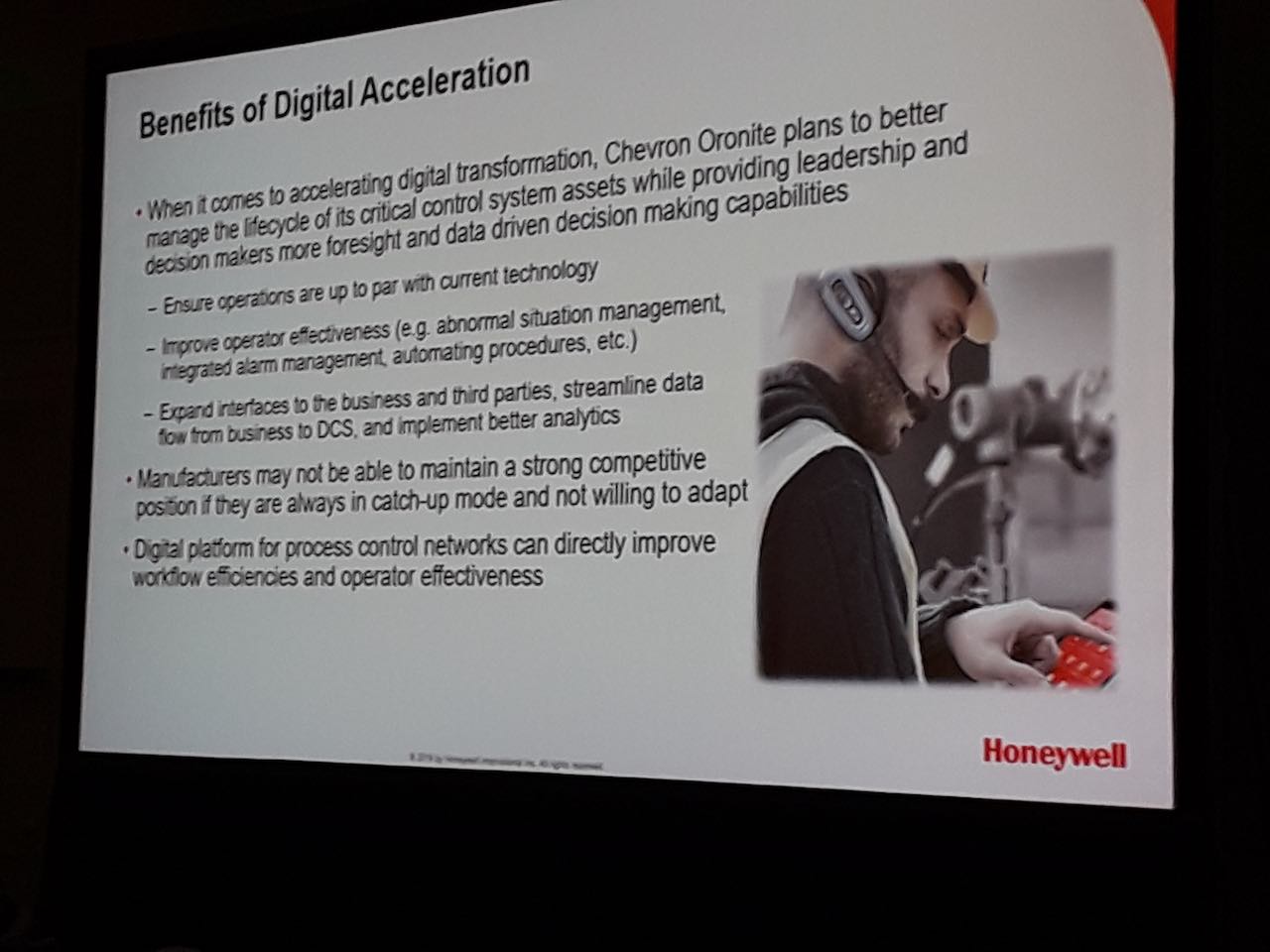
New tools bring digitalization advantages to automation more easily. Your biggest risk, according to experts? Not starting. Yes, change is hard. However, digitalization opportunities are scalable. Don’t wait. Get connected. Get updated. Get more productive. See examples and encouragement below.
Digital acceleration: Demographic mandate
Chevron Oronite modernized its process control system with a focus on digital acceleration, explained Natarajan “Nat” Muthaiah, senior process control engineer, Chevron.
Muthaiaha said his lubricant additive subsidiary wanted to help Chevron achieve digital transformation, to convert data to information and insights to decisions. Yes, it’s disruptive technology, Muthaiah said, by incorporating new process automation architecture, information, cybersecurity, analytics, the Industrial Internet of Things (IIoT), cloud-based intelligence and an agile mindset. But don’t panic, he advised. Start with what you know in the process control space.
New engineers, if found, cannot be taught legacy distributed control system (DCS) technologies. Accept the realities of the new generation and look toward new process control and automation.
Also at Honeywell Users Group Americas 2019 in Dallas in June, Jason Urso, Honeywell Process Solutions vice president and chief technology officer, showed how digitalization advances helps eliminate hundreds of steps in a control system implementation.
Digital technologies converge
Digitalization trends like artificial intelligent (AI), cloud, edge, advanced robotics and others are merging to transform industry, explained Raj Batra, president, Siemens Digital Industries USA, at Siemens Summit 2019, also in June.
Implementations of AI will outpace prior industrial revolutions. Critical industrial assets, including power supplies and terminal blocks can give health advice about their status and attached equipment.
“It’s a mistake not getting started with digitalization,” Batra said.
The technologies are very scalable with fast return on investments. When error detection is applied to machine models for gas turbines, maintenance intervals can be extended 30% with cost reductions. Get the first mover advantage.
For example, in 2018 Fabio Perini North America partnered with Siemens to build and commission a pilot line that initially focused on product testing and development. The project showed how digitalization helped maximize productivity and profits. With the upgrades, and models used in redesign, cabinet space was reduced by 75%. Cloud-based analytical applications give feedback data on the machine to develop continuous improvement. The plant helps Perini customers to develop new tissue products that can maximize productivity and profits.
Among other industry applications, digitalization helps control valve monitoring avoid the high cost of downtime, lowers maintenance costs and decreases risk at a DuPont plant.
Think again about what critical assets could benefit most from digitalization and get started now.
Mark T. Hoske is content manager, Control Engineering, CFE Media, [email protected].
ONLINE extra
Learn more about the Hannover Fairs USA Digital Industry event in September.