Flexible computing, contextual data and modular architectures will change the face of control systems and improve overall plant performance, helping to lower risk from retirements.
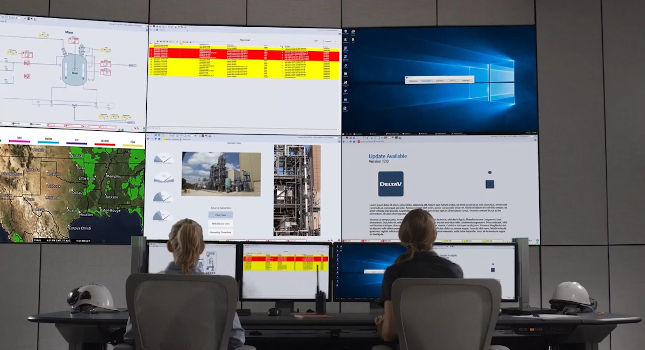
Learning Objectives
- Control system technology improvements can make plant operations faster and safer.Â
- Recent workplace changes due to the COVID-19 pandemic have forced operators to make their control systems more flexible.Â
- Advances in edge computing, digital twins and computing power let control systems make more decisions.Â
Organizations invest in control systems intending that the control systems will operate as intended for many years. However, the pace of change for control systems is accelerating, and the next decade will bring tremendous evolution. Understanding these changes is critical for organizations seeking to secure the best operational performance and return on control system investments.
For decades, the control system was constrained by physical hardware: hardwired input/output (I/O) layouts, connected controllers and structured architectures including dedicated networks and server configurations. Now, the lower cost of processing power and sensing, the evolution of network and wireless infrastructure, and distributed architectures (including the cloud) are unlocking new opportunities in control systems. Additionally, emerging standards for plug-and-produce, such as advanced physical layer (APL) and modular type package (MTP) interfaces, will drive significant changes in the way plants design and use control systems over the next decade.
Even with the changing times and technologies, the equation for success remains the same: choose a reliable, easy-to-engineer control system while providing access to new technologies for improving operations performance.
Control system flexibility mitigates retirement risks
Over the last decade, industry has watched expert personnel reach retirement and has taken steps to mitigate the impact of this loss of expertise. This trend has been exacerbated by recent COVID-19 operating conditions, causing a number of industries to limit on-site personnel.
At the same time, an abundance of new sensing technologies and high-bandwidth transmission options have plants collecting more data than ever, with organizations wanting to extract more value from the data to drive business performance and differentiation. This includes more flexible product delivery capabilities, optimizing quality and throughput consistency, and driving a higher level of operational safety and environmental compliance.
Figure 2: Centralizing data makes it easier for organizations to deploy one-way, secure mobile access to control system data, enabling plant personnel to maintain visibility from anywhere. Courtesy: Emerson[/caption]
Increased computing power enables more advanced control
While it makes sense for some data to move to the cloud for enterprise-level performance-based analytics, other essential data is needed closer to field devices and assets to improve operations and control on the plant floor. Control clusters with high computing power and edge analytics capability will make this shift possible.
This type of edge computing is flexible and adaptable, providing variable control to different parts of the operation to enable modular manufacturing with plug-and-produce technology. The distributed control system continues to orchestrate control across the plant by leveraging a combination of edge computers and control clusters.
In a control cluster, banks of computing power are located in different places across the architecture. Plant personnel can allocate control to any part of the cluster on demand. This provides flexibility for adding software, or for performing upgrades or maintenance. Operators and technicians also can move control to a different part of a cluster while working on part of the infrastructure, ensuring process control continues, even as the plant makes changes to the control philosophy or operational design.
Ease of integration expands efficiency gains
The key to success is to find platforms enabling adoption of new technologies, while minimizing the expense of integration and engineering. The most advanced controllers can operate as standalone controllers and have the capability to natively integrate into a larger control system, enabling organizations to evolve the control architecture and its capabilities, along with processes and product.
Industry leaders also are reducing effort for modular manufacturing implementations with new auto-configuration technologies. MTP technology – developed by the User Association of Automation Technology in Process Industries (NAMUR) –  leverages existing technologies to build an interface to integrate disparate systems in a formulated way, simplifying design of modular systems.
MTP standardizes interoperability between production modules and the control system, allowing plants to mix and match components. The control system will continue to play a vital role in controlling and optimizing these disparate, but more integrated modular systems, and leveraging these integration efficiency standards is a key element for driving the best outcome.
APL, advanced control and digital twins augment operations performance
The control system has historically been used for regulatory control. In recent years, trends have shifted to provide operators with a broader span of control outside of the core operation of the plant. Control systems now encompass a great deal more analytics and decision support to help operators make better decisions across a wider area of responsibility.
Technologies such as APL enable a cost-effective interface to field devices. APL connects I/O to field devices via Ethernet, creating a much faster communication stack. In addition, APL harmonizes the physical layer by deploying one standard physical layer to which multiple protocols can be applied, creating more consistency in how control systems physically interface with field devices.
The ability to see a wider subset of data than was traditionally available will need to be supported with technology to help operators, engineers, and technicians make sense of the data. One key technology expected to see widely expanded use in the next few years is state-based control (SBC).
SBC combines operator-initiated state transitions with automated control logic, enabling operators to help processes achieve optimum operations in any desired state. With SBC, automation technology drives equipment and units based on the current operational state. Operators act as process managers—intervening in the process only when prompted at critical points.
SBC also maximizes the investment in the control system by capturing knowledge in the form of operating discipline users can leverage. It offers reduced training costs, and it drives enhanced safety and operability through the uses of safe states in units, and via communication among units to optimize the response to plant upset scenarios.
Operators will focus more on the bigger picture of processes, monitoring key process indicators and making critical decisions to maintain and improve performance, availability, and quality. Tools such as digital twin simulations – exact virtual replicas of the plant environment – will play a key role in helping operators make the best decisions when a process trends the wrong way (Figure 3).
Instead of making a decision, implementing it, and hoping it was the right choice, operators will instead use simulations to test key decisions in an offline environment.
For example, an operator in a plant may notice a process parameter is trending the wrong way. The operator, using a digital twin tries a new scheme, only to discover it runs too close to the trip limit. Wanting to avoid this scenario, the operator instead tests alternatives using the digital twin and discovers a way to safely bring process parameters back in line. The operator is guided to the correct decision without having to test anything on live processes and equipment. The digital twin will be available on-premise and in the cloud and will be a standard part of most projects.
Practical value remains the priority
The modern control system and cloud computing will provide ways to centralize and contextualize data, enabling small groups of skilled personnel to cover wider geographic areas, while providing superior service. To get the best value from these new solutions, organizations need pre-engineered and easy to deploy automation platforms to help them evolve as market and business conditions change. The control system will always be the brain behind plant operations, but for organizations embracing the upcoming changes, it will also become an enabler for operational success across the enterprise.
Sean Sims is the vice president for Emerson’s DeltaV platform. Edited by Chris Vavra, web content manager, Control Engineering, CFE Media & Technology, [email protected].
MORE ANSWERSÂ
Keywords:Â Control systems, digital twins, edge computing
CONSIDER THISÂ
What control system changes are you hoping will occur in the plant?