By standardizing the data representation of process plant instruments and other devices, the Process Automation Device Information Model (PA-DIM) simplifies access and expands compatibility to transport essential field data up to enterprise computing assets.
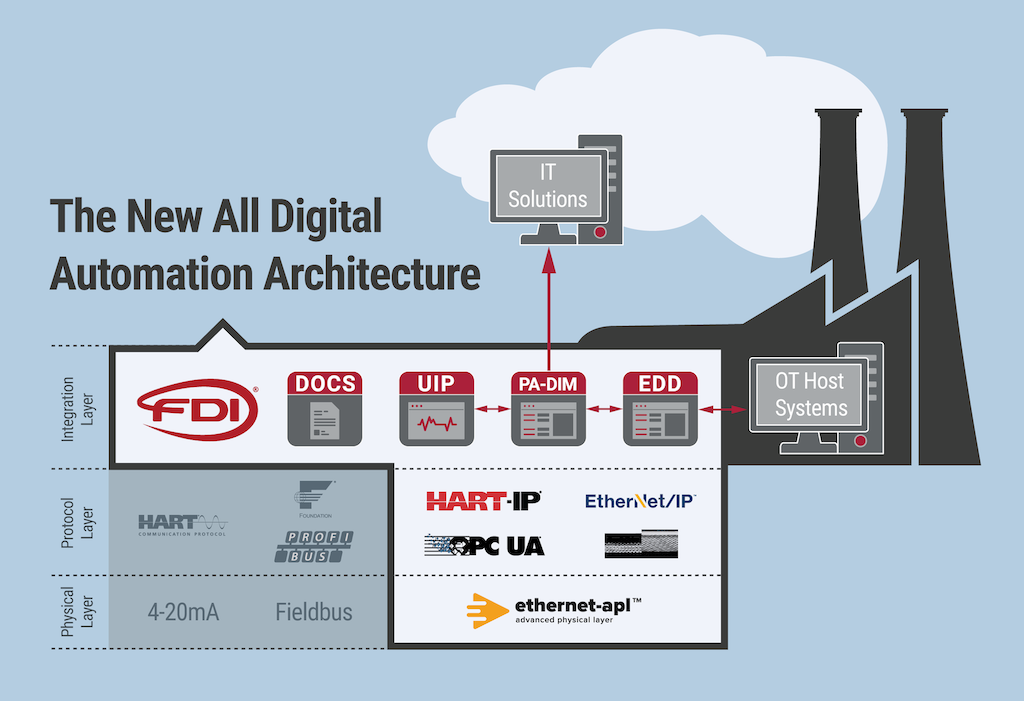
Learning Objectives
- Bridge the great OT/IT divide by examining data sources, such as instrumentation and field devices and using Process Automation Device Information Model (PA-DIM) fundamentals, such as moving data where needed.
- Examine three major benefits for digital transformation, IIoT, OT/IT convergence as well as standards, protocols and harmonization.
- Understand how to deploy PA-DIM and how it simplifies data access.
Industrial communication insights
- Improve OT/IT communications by examining data sources, such as instrumentation and field devices and using Process Automation Device Information Model (PA-DIM) fundamentals, such as moving data where needed.
- PA-DIM offers three major benefits for digital transformation, IIoT and OT/IT convergence as well as for standards, protocols and harmonization.
- Explanations are offered about how to deploy PA-DIM and how it simplifies data access.
Data connectivity within the process and manufacturing industries has achieved great progress over the years, as communications and digital technologies have evolved and combined with user demands for open architectures. This is creating improved interconnectivity options, and designers today enjoy access to a range of best-fit fieldbuses, network technologies and communications protocols for supporting each aspect of an automation project.
However, it is not quite time to celebrate, as there remain challenges to establishing smooth communications throughout an entire operation—ranging from remote field instruments, up to the control room and on to cloud-based enterprise resources. Traditional automation data flow hierarchies demanded rigid and resource-intensive strategies to span these regions while preserving security. However, the modern internet of things (IoT) approach now calls for streamlined plant-wide communications, which must be facilitated by standard information models and provisions for excellent machine-to-machine integration.
For these reasons, FieldComm Group and the OPC Foundation formed a joint working group in 2017 to specify a Process Automation Device Information Model (PA-DIM). PA-DIM is a standardized “information model,” based on OPC unified architecture (OPC UA), and is developed to support industrial applications more broadly by participation from co-owners consisting of nine member organizations. It was established with the goal of creating a protocol-independent way for enterprise computing resources to effectively access field device data. This article introduces how PA-DIM standardizes connectivity from field devices, up through plant networks and control systems, and on to enterprise computing systems (Figure 1).
Bridging the great OT/IT divide
Automation system designers and implementers today recognize that many fieldbuses have a broad installed base for facilitating various aspects of operational technology (OT) plant installations. Industrial OT communication protocols such as Foundation Fieldbus, Profibus, HART and WirelessHART are all installed today. The OT world understands the various physical layers associated with these, the automation protocols used, and the device descriptors (DDs) that define field device information.
The advancement of Ethernet protocols into this environment is now beginning with Ethernet advanced physical layer (Ethernet-APL) for hazardous areas and single pair Ethernet (SPE) for non-hazardous areas. Soon we’ll be seeing much broader adoption of EtherNet/IP (ODVA), PROFINET (PI North America) and HART-IP (FieldComm Group) into the OT world.
Ethernet is also fundamental in the information technology (IT) domain. However, the protocols differ from those used in OT, along with the requirements. The OPC UA protocol is commonly used for enterprise-wide applications. At a plant level, IT understands data connectivity for asset management and historizing. At an enterprise level, IT resources are applied to tasks such as analytics and enterprise resource planning. And for all IT users, security is a top concern.
The wealth of data available throughout OT must be translated to IT to realize value, through various means including analytics, machine learning (ML) and artificial intelligence (AI). Each of these pursuits requires historical and real-time data so they can be employed to drive process optimization, overall equipment effectiveness (OEE) efforts, predictive maintenance, and other efforts.
Data sources: Instrumentation, field devices
Most of the necessary data comes from a substantial installed base of existing instrumentation and field devices. For new installations, meanwhile, it has become clear that there will be no single media and protocol standard suitable for all applications for the foreseeable future.
Even with a focus on openness among systems and protocols, there are plenty of cases where certain types of source data in the field simply do not have a clean path for mapping up to higher level resources that need the information. A system of semantics is necessary so both the sender and receiver of information—typically different OT or IT systems—clearly understand what is being conveyed.
An easy-to-understand example of the importance of semantics can be illustrated as follows. Two people are standing on a busy city street. As traffic zooms past, one says to the other, “Wow, look at the Jaguar coming toward us.” In this context the listener will look to the street an expect to see a beautiful automobile. Now let’s change the setting to a jungle trail, instead of a busy city street. In this context, when the word jaguar is spoken it will have an entirely different meaning—that of a big ferocious cat. Rather than turning to look, the listener would be more likely to turn and run!
Less easy to understand is a similar conversation between machines, or software applications. But the need for rigorous definition remains the same. PA-DIM addresses this need by using existing IEC standards for semantic definitions.
There exists a disparity between the way data is produced throughout OT plant installations, and how higher-level IT systems can consume this data for historical logging, analytical, and other purposes. PA-DIM was conceived to bridge this OT/IT chasm, thus providing a standardized way for communication between OT and IT systems, independent of automation protocols involved.
PA-DIM fundamentals: Moving data where needed
As end users are increasingly undertaking digital transformation projects, they are looking for the best ways to access and transport plant data up to the enterprise. One way they are driving the issue is via NAMUR, which is an end-user member association. NAMUR has published Recommendation NE 175, titled “NAMUR Open Architecture – NOA Concept.” The NOA aims to provide production data to higher-level enterprise computing resources securely and easily so it can be used for monitoring, analysis and optimization. NOA introduces a new monitoring and optimization (M+O) domain, which can work in parallel with more traditional process automation systems.
One of the technical underpinnings necessary to support the NOA M+O concept is PA-DIM. In traditional architectures, smart OT devices are supplied with DD files, which are consumed by OT-centric hosts — such as a distributed control system (DCS) — that understand this format and can use it to interpret what data and functionality is available. However, IT hosts and clients generally cannot use a DD file directly, so PA-DIM was developed to create a software parameterization of OT data, making it suitable for IT.
Three major benefits for digital transformation, IIoT, OT/IT convergence
PA-DIM is a unifying technology standard for digital transformation, IIoT, and OT/IT convergence, providing three major benefits:
• It enables coexistence and cooperation among other technology standards.
• It supplies data context and semantics, greatly simplifying the usage of this data by higher-level computing resources for analytics and other purposes.
• It is a foundational information model for efforts necessary to take full advantage of edge data. Only when data is readily useful is it likely to be applied to obtain value.
In summary, the PA-DIM model provides an avenue for IT systems to easily achieve read-only integration directly with field devices—which may support different automation protocols—exposing the necessary data with full contextual semantics. A basic set of device information is standardized for identification, diagnostics, process variables, device health, and other core parameters.
Devices are uniquely identified by a manufacturer-defined device product instance and a user-writeable alphanumeric asset identification, and they supply many signal tags to a client. PA-DIM is the new information architecture focused on supplying signals with standardized semantic architectures, as opposed to the older method of requiring unique function-centric models for each type of field device (Figure 2).
Standards and protocols, harmonization benefits
By harmonizing with the NAMUR NOA requirements and information model, PA-DIM maps device and semantic information in a standardized way according to IEC 61987. This IEC standard concerns data structures and elements for industrial process measurement and control, and defines concepts such as a common data dictionary (CDD), operating lists of properties (OLOP), and device lists of properties (DLOP). Establishing a CDD, OLOP, and DLOP is essential for enabling IT to access device information without more specific knowledge of the devices themselves.
OPC UA, a secure data transport protocol with strong IT acceptance, is an enabling technology for PA-DIM. Initially, OPC UA and PA-DIM will be used together as a second channel for transporting M+O data from field devices directly up to the enterprise. And eventually, the availability of Ethernet-APL and general OT/IT acceptance of OPC UA as a secure and high-performance contextualized control and M+O protocol may potentially enable OPC UA to support completely open architectures for seamless information flow.
Deploying PA-DIM
As PA-DIM is publicly available and conforms to OPC UA, suppliers and users can use a manual approach to create their own device mappings to PA-DIM by combining published supplier information and specific plant configuration data. But this process introduces a potential for errors and is not very suitable for scaling up to large installations.
A better approach is to use Field Device Integration (FDI) packages enabled with PA-DIM (Figure 3). With FDI, the PA-DIM data is created from the electronic device descriptor (EDD) file associated with the device. OT systems already rely on this EDD file for setup configuration and maintenance of the device, but IT systems do not, they just understand OPC UA. By using FDI, end users are guaranteed that the information used by OT host systems and IT enterprise systems is the same since it is being sourced from the same base EDD file. This reliability is not assured if the device is manually mapped by a user supplier or integrator.
PA-DIM simplifies data access
Once source data is mapped into a PA-DIM model, the data can be readily consumed by IT clients. And as PA-DIM technology is developed further, clients will gain the capability to directly query a PA-DIM server to ascertain what data is available, and then connect to it.
PA-DIM leverages OPC UA’s support for contextualized data, extending this capability with the syntax and semantics needed to contextualize process plant OT field device data points in a manner that makes them easily-understood by IT computing resources. Instrument suppliers using HART and other protocols can map their existing and upcoming devices into PA-DIM today, providing convenient IT access to the valuable data contained within these products.
As digitalization simplifies access to plant floor data, the audience of users seeking value from mining this data expands, and leads to discovery of new insights and operational enhancements. However, the source information must be reliable, accurate, understandable, and consistent throughout all site and enterprise operations. Because OT and IT application domains typically use different protocols, languages, and architectures, it has historically been a challenge to properly align the available data among all target applications. PA-DIM is a technology standard for bridging the gap between OT and IT, in a standardized way using technology that is more familiar to IT-centric users looking to obtain value from process plant data.
Paul Sereiko is the director of marketing and product strategy of the FieldComm Group. Edited by Mark T. Hoske, editor-in-chief, Control Engineering, WTWH Media, [email protected].
CONSIDER THIS
Is industrial data getting from where it’s created to where it’s needed and when?
ONLINE
If reading from the digital edition, click on the headline for more resources.