Digitally transforming operations in the control room can provide new methods for solving problems and improving optimization with increased automation. A refinery projected almost $200,000 in energy savings for five heat-exchangers in 90 days.
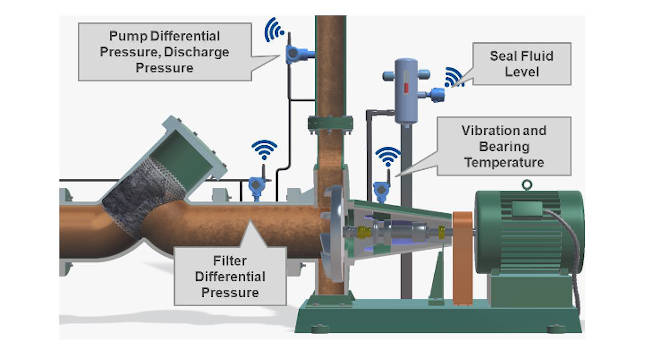
Learning Objectives
- Digitally transforming the control room improves optimization and efficiency.
- Better and centralized data makes it easier to improve equipment performance and schedule proactive maintenance.
- Changing operator behavior and reviewing standard operating procedures (SOPs) can reveal new optimizations.
The refining industry is undergoing a transition period driven by fluctuations in fuel demand, regulations driving net carbon zero targets, and a new sustainability vision. At the same time, the past year has seen the added challenges of COVID-19 and the restrictions it brought, which have put efficiency, worker safety, and automation more into focus. All of these dynamics are prompting refiners to reevaluate their operational strategy to ensure long-term viability. Investments have ranged from refinery conversions to green diesel production plants, the addition of green diesel units to existing refineries, and/or digitally transforming existing operations for positive impact in key performance indicators (KPIs), such as maximizing margin, improving safety, and maintaining availability.
Historically, refineries were primarily instrumented for process control purposes. Adding additional measurements or implementing software solutions beyond process control and optimization models were deemed too expensive. Newer technologies, such as wireless technology and pre-built reliability analytics, are some examples of digital tools that eliminate these traditional challenges and provide new methods to solving problems, optimizing, and executing work practices. One of the focus areas for digitally transforming operations is operator performance in the field and control room.
Compelling reasons to automate operator rounds
In recent years, the need to do more with less has been a common theme; refining is no exception. This means many operators might have more rounds to make than they had before, or they’ve seen their tasks expand to include more.
Manual rounds can be limiting to the process due to data inconsistencies; they are a snapshot in time. Measurements might be missed or not taken as often as needed to create a complete picture of process or equipment health. In addition, if manual data collection is still used, the data may not consistently be uploaded electronically into a database, so the data is not used other than verifying an obvious difference from a previous reading.
This also means potential problems might not get flagged or caught early. The benefits of automating operator rounds go beyond reducing personnel time in the field or a faster, continuous data collection process. The real benefit comes from leveraging the value of the data for process optimization and to transform work practices, such as moving from preventive maintenance to predictive condition-based maintenance (CBM).
Improving equipment performance
One of the areas for automating and analyzing data collection involves health and performance monitoring for critical assets such as pumps, heat exchangers, pressure relief valves, corrosion monitoring, and steam traps. Implementing a second layer of automation with wireless sensors for level, temperature, pressure, vibration and acoustics provide cost-effective, continuous measurements for previously-checked or unmeasured variables. The devices can now be wirelessly tied to a central dashboard and equipment monitoring software solutions that allow for the collection, aggregation, validation, and analysis of the equipment health and process data.
This means a system can be set up to send the relevant data to specific departments such as reliability and maintenance, which will most benefit from the information: people who can analyze the data, spot trends, or flag possible issues. Better and centralized data makes it easier to improve equipment performance and schedule proactive maintenance instead of being reactive when something goes wrong. The equipment health data also ca improve safety by avoiding unnecessary maintenance and detecting issues that could result in high-risk conditions or unplanned shutdowns.
For example, many refineries have implemented monitoring solutions for heat exchangers. As refiners have processed more discounted opportunity crudes, including some they have little experience processing, accelerated or unpredictable fouling of crude unit heat exchangers has become an issue, resulting in energy inefficiencies.
Moving beyond costly traditional maintenance, $200,000
Traditionally, operators would either follow a scheduled maintenance routine to clean heat exchangers or rely on valve output changes or manual readings to determine when a heat exchanger needed cleaning. However, it is possible to add process measurements such as temperature, flow and differential pressure, and combine heat exchanger design data into pre-built analytics to determine calculations for heat exchanger fouling, heat duty monitoring, cleaning recommendations based on high fouling, and high differential pressure.
These calculations can then be configured to alert process unit engineers, energy efficiency teams, as well as reliability and maintenance departments of performance issues so they can shift to preventive and prioritized maintenance. Furthermore, a fleet of exchangers can be aggregated to view the health of all assets and enable an overall snapshot and prioritization of exchangers in the plant.
One Gulf Coast refinery projected almost $200,000 in energy savings for five heat-exchangers in their crude unit preheat train in 90 days. Prior to implementation, the refinery lacked information that prevented economic analysis planning for fouling degradation verse additional fired heater fuel.
Adding real-time wireless temperature tube bundles and pre-built heat exchanger modeling software enabled the refinery to plan for a more optimal cleaning schedule. The heat exchanger payback period ranged from 50 to 90 days for each exchanger.
Improving work practices, $500,000
Beyond equipment performance and maintenance, automating operator rounds can extend beyond data collection to implementing more efficient digital work practices. For example, for environmental regulatory reporting, emissions reporting may require refiners to include unit charge rates for greenhouse gas emitters like the fluidized catalytic cracker, coker or reformer, as well as utility water consumption.
Typically, the regulatory agency will often require plants to meet accuracy specifications for the flowmeter as well as a calibration every few years to ensure the accuracy of the meter is maintained. Meters would often have to be pulled from the operation and sent to a calibration facility for verification and recalibration.
Today, some transmitters for Coriolis and magnetic flowmeters can have automatic meter diagnostic software that monitors the meter’s performance and integrity without stopping the process and eliminates the need for scheduled visits to the field. The meter verification testing can be scheduled, and automated reports can be generated to demonstrated compliance to accuracy and inspection requirements set by agencies in lieu of some or all calibrations and provings.
Another area of improvement involves annual steam trap audits. The audits are often handled manually and using input of flow through acoustic noise and temperature to analyze each operating trap compared to ideal parameters. Getting steam trap audits that consistently reflect the actual health of the system is a problem due to operator interpretation of flow noise and a small inspection time that can be as little as 15 seconds per trap.
For example, a large refinery recently installed 50 steam trap monitors and was skeptical the permanently installed real-time monitoring system would be more accurate than their manual audits done once a year. They believed their manual inspection system was 95 to 97% reliable. After installing wireless acoustic monitoring around 24 steam traps found to be in good working condition during the manual audit, they found 16 traps were in a failed condition. A third party checked the validity of the traps and confirmed the 16 traps were in failed condition. The financial impact more than $500,000 per year if these 16 traps were not repaired.
Improving operator performance
Improving operator performance goes beyond digitizing and automating work practices in the field and can be extended to improving performance in the control room as well. First, a review of standard operating procedures (SOPs) should be conducted to see if behavior should be changed or updated to reflect to new technology enhancements. Second, industry best practices and benchmarking data can be used to reassess and optimize performance to match today’s operational needs. A consultant can first benchmark a refiner’s operation against industry standards, covering areas such as alarm management, fatigue risk management, human-machine interfaces (HMI) for control systems and how effectively procedural automation is utilized when transitioning between states of operation.
For example, how well a distillation column automatically transitions from shutdown to warm up to total reflux to run. The consultant benchmarking evaluation will lead to sound recommendations for improvement.
Improvement recommendations include operator workload different behavior from the field operator including SOP changes.
With the example of wireless pump monitoring, the field operator no longer needs to manually collect process and vibration data to decide if maintenance is required; the data is automatically collected online, stored, validated, analyzed and set to alert an operator if degrading or imminent failure is expected.
The field operator can now check equipment visually and audibly for abnormalities, such as higher noise or leakage, rather than collecting data. Also, since the data is collected and processed automatically, maintenance can be planned based on condition-based rather than time-based strategies.
Rounding up the process efficiency benefits
Automating operator rounds has several benefits such as safety, less time spent in the field, and increased process efficiencies. Automation of periodic equipment inspections or field sampling points provides benefits beyond efficiency. The aggregation and trending of the data provides consistent, real-time performance indicators and alerts of issues that used to result in unplanned shutdowns, energy losses, or maintenance.
The workload transformation doesn’t stop in the field. Industry benchmarks and best practices can be used to evaluate operator performance in the control room, as well. Holistically approaching operator performance and leveraging digital technologies and tools in the field and control room can provide a well-rounded approach to improving operator efficiency and performance.
Meha Jha is a refining industry marketing manager for Emerson’s measurement solutions business. Tim Olsen is a control and operator performance business development manager at Emerson. Marcio Donnangelo, global business development at Emerson. Edited by Chris Vavra, web content manager, Control Engineering, CFE Media and Technology, [email protected].
MORE ANSWERS
Keywords: process manufacturing, digital automation
CONSIDER THIS
What benefits would your facility gain from digitally enhancing operations?