Input/output (I/O) systems design considerations include smaller sizes, faster response times, and greater functionality, with energy savings, diagnostics, and rugged environmental ratings.
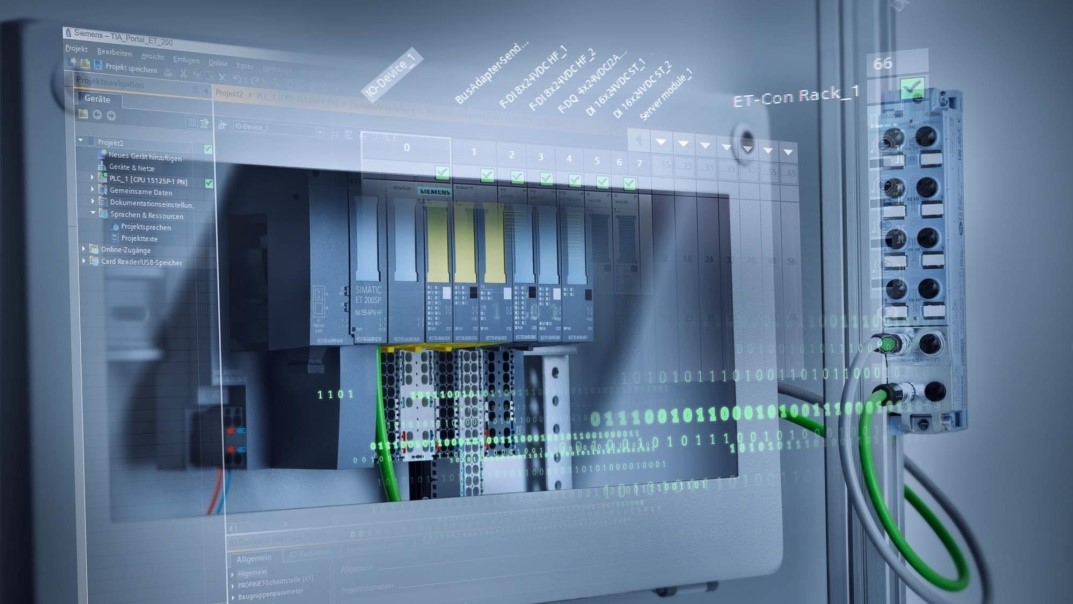
Input/output systems (I/O or IO systems) are designed to be simpler, smaller, and more powerful. Installation and wiring should be simple, done faster, and with fewer or no tools. Compact size, faster response times, diagnostics, and greater functionality are expected.
Such designs help companies are being challenged to meet ever-changing demands from the marketplace in more competitive manufacturing environments. They are pushing their automation systems to maximize performance, improve efficiency, increase flexibility, and reduce downtime while reducing the automation system’s overall footprint. To meet these challenges, automation that’s smaller, more powerful, and offers greater functionality is needed.
The cabinet-based IP20 rated stations are offered with extensions to cabinet-free IP65/67-rated I/O stations. Stations have increased energy efficiency with just the right quantity of I/O, with the possibility for expansion. Diagnostics are available at the human-machine interface (HMI) level and right at the module with LED lighting for each channel.
The I/O system offers a wide range of I/O types from simple I/O to feature rich, high-speed I/O that can detect and report system diagnostics in detail and support higher performance for high-speed machines. Intelligent I/O and fail-safe I/O in the same system are demanded.
I/O stations with reduced parts variance bring major cost savings. Color-coded and numbered terminal connections make installation quick and easy.
Industry-standard connection methods with copper and fiber cables and multiple ports for station extension are required.
Multiple communications
While connecting to a controller via an industry standard fieldbus network, the station also has the capability to communicate to simple fieldbus devices used in the industry. Technology functions such as high speed counting, positioning, camming, condition monitoring, and weighing make the station attractive to complex machine applications.
Advanced users also demand I/O processing beyond the I/O cycle time of the controller with functions such as time stamping, oversampling and module-to-module (M2M) communication. Energy metering and reporting also has greater importance to management conscious of corporate energy costs.
Another industry trend is to have the I/O station in central configuration with a CPU and distributed. This allows them to have machines built with their own control functions and the ability to network them to other control and monitoring stations.
Some users require I/O stations to handle extreme mechanical and environmental conditions. The user benefits from using the same hardware and software for specialized hardware that is transparent to the application developer.
Customers also expect a product lifecycle management policy to support the hardware for an extended period of time after the product is phased out.
While I/O systems differ, suppliers should be committed to constantly improving I/O system products to enable users to optimize their automation systems for a competitive advantage.
Raj Rajendra is consultant/manager, Siemens Industry Inc. Edited by Mark T. Hoske, content manager, Control Engineering, CFE Media, [email protected].
KEYWORDS: I/O systems, I/O stations
Input/output (I/O) systems while compact, are expected to have faster response times, and greater functionality.
Energy savings, diagnostics, and rugged environmental ratings are among I/O system needs.
Hardware support for I/O systems is expected 10 years after phase out.
CONSIDER THIS
If I/O system controllers had faster response times, more functions, and smaller size, how would that help?
ONLINE EXTRA
Siemens provides more information about the products below.
See related New Products for Engineers at www.controleng.com/NP4E