Automation is a necessity for manufacturing facilities, and it starts with gathering data and understanding where it is (and isn’t) needed and what technologies can help maximize return on investment (ROI).
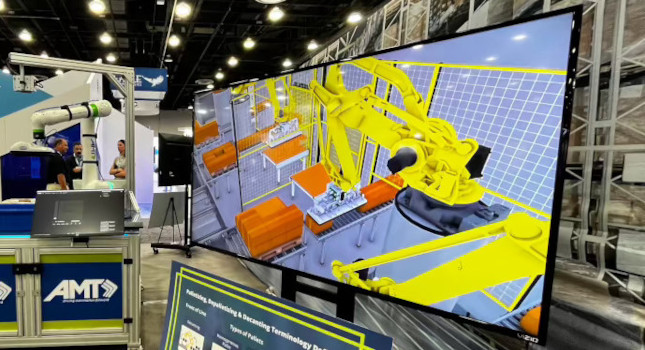
Learning Objectives
- Automation is becoming a necessity for manufacturers due to supply chain issues and severe labor shortages.
- Industry 4.0 adoption is making automation possible for technologies that wouldn’t have been considered even a few years ago.
- Younger workers are embracing technology and automation in their daily lives.
Automation Insights
- Automation has gone from being a buzzword to a necessity in manufacturing. While it was originally designed to take away the dull, dirty and dangerous jobs from people, it has become more than that. Now, manufacturers realize it’s a “must have” if they want to stay in business.
- The increased use of interactive technology, thanks to the Industrial Internet of Things (IIoT), makes these jobs more appealing to younger workers. They expect – and even demand – technology to play a key role in their jobs.
Recommending automation is a data-driven process and will often make it very clear if automation is a wise investment, or not, based on the customer’s goals and targets. Combining prioritized objectives with sound data, it becomes much easier to make intelligent decisions backed by a strong business case or return on investment (ROI).
In the past, when AMT visited a manufacturing facility and conducted an audit, we looked to automate tasks that were one of the “four Ds”: dull, dirty, dangerous, or difficult. Traditionally, the 80/20 rule was applied to automation; there usually wasn’t a strong business case for implementing automation if we couldn’t capture 80% of what a customer was producing. If a customer had a chaotic product grid or process, automating 80% of production often became too expensive for automation to make sense.
More recently, advances in automation technologies and labor shortages have changed former industry assumptions and the business case about what should or shouldn’t be automated. Now, customers are often saying they need to automate, or they will not survive because the extra labor needed to process additional throughput isn’t available or workers don’t want to do certain types of jobs anymore.
Consider someone in the welding profession: if it’s a 100-degree summer day, the big helmet and heavy protective clothing makes the welder hot and uncomfortable all day while performing a dirty and difficult job. Meanwhile, this worker could get a more comfortable desk job, which has resulted in people in leaving or not considering jobs such as welding, creating labor deserts in many industries.
These days, automation is not about replacing people with machines or reducing labor; it’s about meeting customer demand for more product without the ability to increase the size of the workforce. It’s about helping some of these companies automate to stay alive or continue to grow when there’s no available labor to fill these roles.
Know where automation makes sense
Data collection is the first step in evaluating the case for automation. This requires the integrator to be at the customer’s site for several days to learn the process and product even better than the customer. The facility visit yields hundreds of photos, reams of data, and a firm understanding of the client’s process, organizational priorities, and constraints, such as increased throughput, increased quality, or budget for capital equipment.
Target setting follows data collection and is arguably the most important step in the process. Engineers should meet with the customer’s team to assign a priority level to each of the customer’s goals or targets. Using this prioritized list and the manufacturing data, an automation roadmap is developed which addresses the customer’s needs, looking at the process as a whole and ensuring there is a strong business case for implementing each recommendation.
Industry 4.0 is leading to more flexible technologies
Adoption has increased as technologies have become more flexible and easier to reprogram. This is a change from even a few years ago when there were certain applications no one would touch with automation because it was not possible to succeed with the prevailing state of technology. Many of the applications considered concepts or R&D projects are starting to enter mainstream production.
Original equipment manufacturers (OEMs) have been working to make products more user-friendly, adopting consumer-products-driven features like plug-and-play technology and enhanced visual interfaces. Many industrial devices can now be programmed by the average layperson without a special education in programming, allowing customers to have an internal subject-matter expert rather than having to hire an outside programming resource for certain changes.
An example of this is with new technology for depalletizing a random pallet or palletizing random products, a task which would not even have been imaginable five or ten years ago. Today, a robot and vision system coupled with a unique software algorithm allows the labor to be removed from this physically demanding task. The new technology’s artificial intelligence (AI) and machine learning (ML) are opening the market by removing the need for human intervention to reprogram the system each time an unknown product arrives on a pallet or comes down the conveyor belt. This reduces the physical labor of a human lifting the products and removes the engineering labor for reprogramming the system for each new product.
Younger workers embrace automation
Each successive generation seems more comfortable and more willing to work with and around technology. Millennials and generation Z, the youngest generation, view technology as a tool to prevent them from having to do the “four Ds” rather than as something that could take their jobs. These workers would rather be programming a robot than doing the manual job themselves. Considered from this perspective, automation provides an opportunity to make work more rewarding, interesting and safer.
Chris Clayton is advanced manufacturing engineer at Applied Manufacturing Technologies, a CFE Media and Technology content partner. AMT is a member of the Control System Integrators Association (CSIA). Edited by Chris Vavra, web content manager, Control Engineering, CFE Media and Technology, [email protected].
MORE ANSWERS
Keywords: automation, Industry 4.0
ONLINE
See additional IIoT and Industry 4.0 stories at https://www.controleng.com/iiot-industrie-4-0/
CONSIDER THIS
How is your company embracing automation and what changes has it led to?