CAN in Automation (CiA) members have developed the CAN XL data link layer specification, which provides the functional and procedural means to transfer frames between nodes and to detect errors that occur in the physical layer.
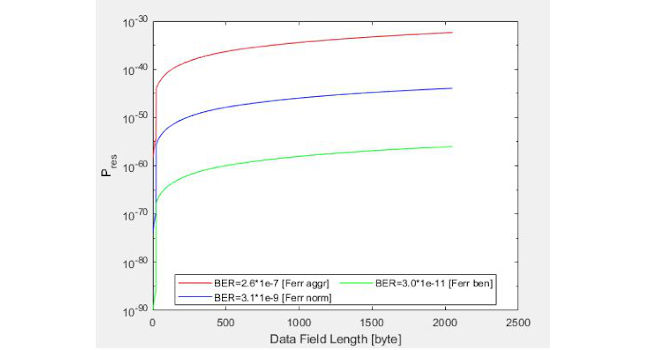
The Institute of Computer-Architecture and System-programming (ICAS) of the University of Kassel has examined the CAN XL data link layer protocol specified in CiA 610-1. For more than half of a year, Prof. Dr. Josef Börcsök and his team investigated in the evaluation of the error detection mechanisms provided by the CAN XL protocol. The final research report comprises a qualitative evaluation of the residual error probability, too.
CAN in Automation (CiA) members have developed the CAN XL data link layer specification. It is available in the CiA 610-1 CAN XL data link layer and physical signaling document. The data link layer (DLL), also known as layer-2 in the Open System Interconnection (OSI) model, provides the functional and procedural means to transfer frames between network entities (nodes) and to detect errors that occur in the physical layer. Frames or DLL protocol data units (PDUs) do not cross the boundaries of a network segment. Inter-network routing and global addressing are higher-layer functions, allowing data-link protocols to focus on local delivery, addressing, and media arbitration. In this way, the DLL is analog to the neighborhood traffic police; it arbitrates between parties competing for access to a medium.
CAN XL, the third CAN generation, features two CRC polynomials, stuff-bit checks, and frame format checks to detect errors in CAN XL frames. In the summary, the researchers concluded: “The CAN XL protocol improves reliability by using cascaded Cyclic Redundancy Checks (CRCs). In that, the MAC frame has two CRC fields: the 13-bit Preface-CRC (PCRC) and the 32-bit Frame-CRC (FCRC). The CRCs are cascaded so that the FCRC also protects the PCRC. Together, both CRCs can detect any five randomly distributed bit errors.”
This compares with a true Hamming Distance of 6 with no shortcuts. “The format checks and the stuff-bit checks additionally ensure the detection of errors in a frame,” the researchers said. “Here, not only the errors in the format fields and in the stuff bits are recognized, but partly also the errors in the remaining bits, which can entail the corruption of the values in the format fields and stuff bits.”
The researchers developed new formulas for the residual error rate (RER) calculation, in order to cover the extended error detection measures in CAN XL. With them you can calculate the RER for a given CAN XL network. The figure shows an example as provided in the research report.
The researchers said, “That due to the worst-case assumptions of the values of some parameters in the development of the formula, as well as in the calculation of the final values, a pessimistic estimate of the RER” is given. This means, the calculated RER values are conservative.
To make the estimation of the upper bound value more precise, the channel model can be improved, to match better to the errors that occur in a specific environment, like burst length, duration of a glitch, and bit error rate. Further the estimation can consider more features of the FCRC and PCRC polynomials. When using the formula to calculate the values, it should be considered that the FCRC for the block length of up to 274 bit features a minimum Hamming Distance of 8. For block length with more than 275 bit, the Hamming Distance is in minimum 6. This means, five randomly distributed bit errors are detected.
“The report concludes that CAN XL is at least as reliable as competing network technologies,” said Holger Zeltwanger, CiA managing director in a press release. “This is a very conservative estimation.”
– Edited from a CAN in Automation (CiA) press release by CFE Media. CAN in Automation is a CFE Media content partner.