Automation is revolutionizing testing and manufacturing facilities, but the increased complexity of designing and integrating automated systems can pose significant challenges for manufacturers.
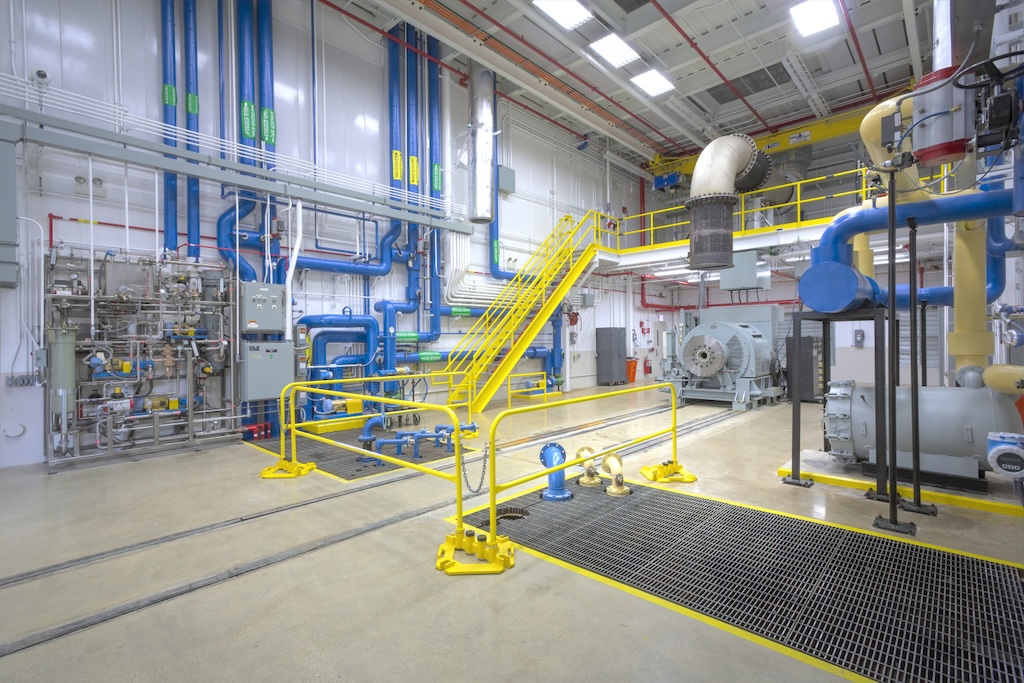
Learning Objectives
- Understand the critical role of front-end planning and systems integrators in designing and implementing optimized automated systems in testing and manufacturing facilities.
- Identify and analyze four key automation trends — modernizing aging production lines, advanced data collection, simulation models and heightened cybersecurity — and their impacts on process modernization.
- Learn the importance of a balanced approach to automation integration, recognizing the potential risks and benefits while avoiding inefficient and costly patchwork systems.
Automation and system integration insights
- Automation enhances efficiency and safety in manufacturing, but its complexity necessitates strategic planning. A skilled systems integrator is key to maximizing automation’s full potential and benefits.
- Modernizing outdated production lines requires adopting flexible technologies like AMRs and cobots. A systems integrator can guide manufacturers through upgrading while minimizing risks and costs.
- Front-end planning (FEP) helps companies design tailored automation systems by aligning technology choices with business objectives, improving integration and ensuring optimal resource allocation.
Automation is transforming testing and manufacturing facilities. It’s being used to streamline processes, enhance precision and repeatability and improve operator safety. However, the increased complexity of designing and integrating automated systems makes it challenging for manufacturers to realize their full benefits.
The role of a systems integrator is crucial to helping companies navigate the available automation hardware and software options while considering the concurrent pull of automation trends and company goals and constraints.
Companies that start the process with equipment selection often end up with an inefficient patchwork system that’s more expensive to build and maintain. They lose the opportunity to design an optimized, automated system where all components work together as a harmonious, cost-efficient solution.
Four automation trends pushing process modernization
For these reasons, it’s vital to start with front-end planning guided by a systems integrator experienced in assembling optimized and automated subsystems. This approach increases the organization’s opportunities to maximize its return on the investment in automation.
Trend #1: Modernizing aging production lines
Many manufacturing companies struggle to integrate modern technologies into outdated systems in facilities and production lines that were built decades ago. Manufacturers often do not have the bandwidth to become familiar with the latest tool advancements.
Without understanding the evolution from automated guided vehicles (AGVs) to autonomous mobile robots (AMRs), they may follow a path that adds constraints rather than alleviates them.
AGVs require extensive infrastructure, including underground sensors and power systems. In contrast, AMRs provide greater flexibility because they’re not physically integrated with the facility.
Other advances in robotics offer still more choices for effectively modernizing a facility or production line. For example, collaborative robots (cobots) provide a flexible, cost-effective option to handle simple tasks safely around human operators. Their limited payload and slower speeds mean they’re not always the right choice, however.
More sophisticated safety sensors improve robots’ spatial awareness and allow real-time environmental mapping to detect potential unexpected obstructions, letting them operate in smaller buffer zones (see Figure 1). The growth of EtherCAT, with its high-speed communication and precise synchronization, is another advanced technology that offers significant benefits but can come with implementation challenges in existing facilities already built around different hardware communication architecture.
Modernizing an aging facility requires a well-considered plan that uses experience to balance objectives, risks and costs. Questions to consider include whether a complete retrofit is necessary, if a staged implementation makes sense and how existing equipment and its alternatives should be assessed for an upgrade. A systems integrator with the right expertise can assist in reviewing and updating project specifications with emergent technologies, providing manufacturers with a strategic plan that helps them navigate this complex decision-making process.
Trend #2: More and better data
Advanced sensors are revolutionizing data collection, providing more precise measurements, greater control resolution, and an increasing variety of data points. This wealth of information enables manufacturers to refine processes for peak efficiency and close the loop in R&D test cycles, iterating designs more rapidly. A growing selection of improved data processing and analysis tools, often incorporating artificial intelligence (AI) and machine learning, transform raw data into actionable insights. These systems can automate experimentation processes, predict maintenance needs and provide analysis for optimizing production lines in real time.
Trend #3: Simulation models
Simulation models are a valuable tool for mitigating risk and lowering costs in automation projects. These models help manufacturers validate expected outcomes and identify design gaps where they have the greatest latitude to make the optimal performance modification for the lowest price. They also serve as a reference point for installed equipment. Building effective simulations demands both process knowledge and expertise in simulation technology.
This expertise involves translating traditional engineering knowledge into sophisticated simulation models aided by complex software. Experience in simulation development also helps the systems integrator determine whether a simulation model would add value to a project because not all projects need them. With this in mind, finding the right systems integration partner requires careful research and vetting.
Trend #4: Heightened cybersecurity imperative
As industrial facilities become more automated, integrated and data-driven, they turn into attractive targets for cybercriminals. Dragos, an industrial cybersecurity and intelligence firm, found that of the cybersecurity alerts it analyzed in 2023, 53% could cause the loss of visibility and control over operational technology (OT) networks (see Figure 2). This is a 51% increase over the previous year. A 2023 cyberattack on Clorox caused operational downtime, resulting in an ongoing loss of hundreds of millions of dollars due to reduced production and lost market value.
The escalating threat landscape for OT networks reinforces the need to conduct regular cybersecurity assessments for all new projects and ongoing facility maintenance to maintain a solid defensive posture. When considering an automation technology upgrade, the planned topology and architecture must be designed with security as a priority. Software and hardware is selected to achieve the required process performance at the lowest acceptable risk of cyberattack.
Front-end planning is the cornerstone of successful automation integration
Every process and application has its unique aspects, making predefined or off-the-shelf solutions inadequate for addressing any individual company’s specific needs or constraints. The vast array of available automation technologies, platforms and equipment complicates the selection process, necessitating careful planning and expert guidance before buying equipment or entering the design phase.
Starting with a front-end planning (FEP) phase is a critical step. FEP is a structured approach to defining project requirements, assessing feasibility and outlining high-level solutions before committing significant resources. An effective systems integrator facilitates a conversation with company stakeholders to fully explore the following key considerations:
1. Current capabilities and preferences. This includes documenting existing infrastructure, preferred vendors, and equipment. An example of which is assessing whether the facility has sufficient electrical capacity to power more expansive automated systems.
2. Specific process requirements. It is essential to understand what the company needs to accomplish in its R&D or production line for a given product. This involves detailing the desired outcomes and ultimate performance metrics.
3. Process complexity. Evaluating the intricacy of the desired automation helps determine the appropriate level of technology and expertise required.
4. Comparison with existing systems. Assessing how different or similar the new process is to existing ones can inform decisions about integration and potential compatibilities.
5. Data requirements. Determining what data and data flows are needed to support design validation, process control and maintenance is fundamental to shaping the automation strategy (see Figure 3).
The FEP process helps organizations right-size their automation efforts, using existing technologies where appropriate and customizing solutions where necessary. It enables organizations to identify potential risks early, optimize resource allocation and ensure alignment between automation initiatives and business objectives. FEP also provides a framework for evaluating the economic viability of different approaches, potentially saving time and money by identifying suboptimal or insufficient options before significant resources are allocated.
Harnessing FEP for strategic decision-making and optimal outcomes
FEP produces crucial documentation that serves as a powerful decision-making tool. It includes the system integrator’s analysis of trade-offs that stakeholders can use to assess various automation design scenarios, each presenting a different balance of costs, benefits and risks. This comprehensive evaluation enables organizations to make automation equipment and design choices, considering factors like compatibility with existing systems, integration challenges and facility constraints (see Figure 4).
The FEP documentation also captures historical knowledge about facilities and existing systems, ensuring critical information is preserved and used effectively. This approach prevents the ongoing risk of piecemeal equipment acquisition, where incompatible automation components might be purchased without considering how they’ll integrate. The final deliverable from any FEP study that passes the viability checkpoint can take two forms: A fully defined automation solution ready for the design phase or a compelling business case for project advancement.
A skilled systems integrator could still implement automation upgrades without going through the FEP process, but this ad hoc approach is more likely to fall short of optimal results. It might steer the company toward the desired outcomes for automating the process but at a higher cost and likely without achieving the valuable outputs and potential customizations. Conducting an FEP phase builds the foundation for the seamless integration and optimal performance of automated systems within the existing facility and network infrastructure.
Balancing modernization and risk in automation
Manufacturers react differently when faced with the surge of automation technologies and potential benefits. Some adopt every new technology without assessing the integration risks or dependencies. These companies find themselves with expensive, fragmented systems that underperform. More risk-averse companies prefer not to fix what they don’t consider broken. The cost of their complacency is falling behind those organizations reaping automation’s competitive benefits.
The more balanced, measured approach lies in the middle. Manufacturers can implement automation by engaging in FEP with a systems integrator. FEP secures the design of an automated subsystem that aligns with the company’s budget, goals and constraints.
A systems integrator specialized in automation technologies ensures interoperability among various systems and facility infrastructure. The result is a system that unlocks automation’s full potential for streamlined processes, enhanced innovation and quality and profitability.
Andrew Harris is director of business development, instrumentation and controls; Matt Thiel is director of facility planning and integration for ACS.