Technology update: Optimization is among key trends for manufacturing and process facilities highlighted in the media session at ARC Forum 2019.
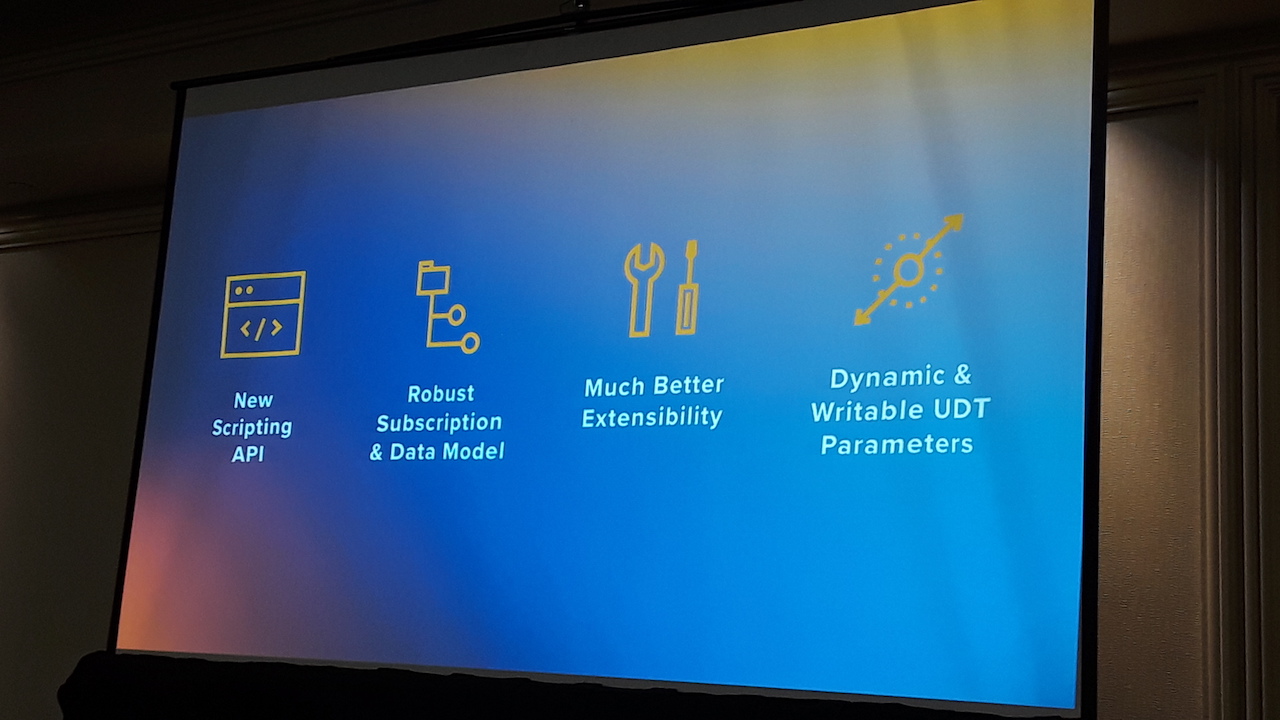
Manufacturing and process facilities are taking advantage of trends in optimization to make their applications more efficient, with lower risk, greater profitability, and more flexibility. Highlights from 2019 ARC Forum media meetings reflect trends driving new product announcements.
Engineering intelligence: L&T Technology Services
Samir Bagga, chief marketing officer and Akshay Chandra, senior manager, strategic marketing initiatives at L&T Technology Services, discussed the need for smarter factories with wireless material tracking, machine vision-based quality inspection, digital twins, energy optimization, collaborative robotics, integrated 3-D modeling, and virtual reality.
Chandra, an electrical engineer, offered some application metrics.
Wireless material tracking with radio frequency identification (RFID) tags on one manufacturing line increased productivity 30%, parts availability 40%, and annual savings by $100,000.
Machine vision for quality inspection increased productivity 8% and lowered reject rates 20% for $150,000 annual savings on one line.
Digital twin implementation improved overall equipment efficiency (OEE) by 13%, decreased inventory by 40%, and saved $1 million per year.
Paperless factory implementation increased productivity 15%, decreased rework 10%, and decreased material waste by 4%.
Energy optimization: Yokogawa
Satoru Kurosu, Yokogawa director, executive vice president, premium solutions and service business headquarters, and Oscar Santollani, senior vice president, visual MESA software business at KBC (a Yokogawa company), discussed how to address energy-related carbon emission reduction goals with end-to-end energy optimization software. Such software uses analytics to help reduce costly uncertainty in energy planning, scheduling, and trading over multiple time periods.
Kurosu sees opportunities in helping with more efficient use of energy to reduce carbon-based emissions with a call to action for approximately $32 trillion in existing assets.
Power generation and industry account for about 60% of energy related CO2 emissions, he said, and Yokogawa can help industry achieve energy optimization to decrease consumption, support the transition to renewables for attention to the supply and demand sides of the equation. Existing tools and techniques can help customers realize more than 10% savings in energy optimization.
Santollani said better forecasting creates better decisions. Software that improves through behavior modeling and variable prediction creates more optimal operating conditions. Cloud interfaces bring in more inputs such as fuel prices, market prices, and the weather to improve operator decisions.
Automation platform: Inductive Automation
Don Pearson, chief strategy officer, and Carl Gould, co-director of software development for Inductive Automation, said an industrial automation platform should integrate web technologies, enterprise-empowering features, and a next-generation visualization system. Doing so can create appealing, mobile-responsive industrial applications that run natively on any mobile device and web browser.
Inductive Automation’s Ignition Perspective module helps users apply automation where they are in a way that the workforce expects; more than 1000 beta users tested the software since October 2018. Mobile apps stores and the URL has a demo, as explained at ARC Forum 2019. https://Demo.inductiveautomation.com. Courtesy: Mark T. Hoske, Control Engineering, CFE Media[/caption]
Pearson noted seven ways software can make automation easier:
- Improve operational efficiency enterprise-wide.
- Licensing with unlimited tags gives system designers more options.
- Unlimited scalability for easier use to multiple sites.
- Large scale data collection and a reliable way to push data to where it’s needed.
- Top to bottom security.
- Operational technology (OT) and information technology (IT) convergence with database-centric software, integrated security, and use of standards and services.
- Modular architecture, easy to adapt to application needs.
Wireless monitoring: Baker Hughes
Kimberly Murphy, executive vice president, hardware, at Bently Nevada, part of Baker Hughes, a GE Co., discussed how wireless technologies can resolve condition monitoring plant-wide machinery issues. An edge-to-cloud approach to asset protection and condition monitoring provides greater safety, uptime, and efficiency, and new levels of productivity and control.
Wireless sensors for condition monitoring can measure vibration in three axes and temperature with greater communication distance and longer battery time than previously possible. Offshore oil platforms as well as other oil and gas applications, power industries, food and beverage, mining, pharmaceuticals, and municipal water applications also can benefit from wireless sensors.
On-premise, cloud, or hybrid: Aveva
Craig Hayman, CEO, Aveva, discussed developments since Aveva’s merger with Schneider Electric’s industrial software business in 2018, such as the progress of digital industrial transformation, and upgrades to visualization products through its cloud subscription model. Formed 12 months ago, the combination of Schneider Electric and Aveva software products resulted in annual revenue of $1 billion. The company designed the latest update to provide its customers with greater flexibility in licensing, configuration, and deployment.
Hayman said digitalization is increasing in the industrial world, according to annual reports and industry discussions. Industrial tendencies include downward pressure on capital and operational spending, a complicated operations environment, multiple MES systems, many applications, and continuous changes. Data, information, and knowledge can provide context users need at the right time. Machine learning and analytics make data into actionable information. That allows companies to run analytics and savings back to the customer with edge to enterprise software and enterprise technologies economically and to scale.
Technologies can enhance assets, extend to the enterprise, leverage edge, Industrial Internet of Things (IIoT), analytics, augmented reality (AR), virtual reality (VR), and cloud-based software. Hayman said the costs of cloud computing infrastructure is rapidly dropping, creating a transformative moment for the industrial sector.
Control and visualization software, Hayman said, should:
- Provide operational and performance insights through enterprise agility.
- Break down departmental silos and bride gaps between IT and OT to integrate simulation with operations design in brownfield and greenfield installations.
- Move with speed, certainty, and less risk. Faster insight, depending on application needs can be on-premise, in the cloud, or a hybrid software. Greater connectivity eliminates data lakes across environments. Subscribe to software to meet capabilities required and scale as needs require.
Safety, profitability: Schneider Electric
Chris Stogner, director of Schneider Electric’s EcoStruxure Triconex safety offering, and Farshad Hendi, global safety practices leader for Schneider Electric’s Industry Services business, discussed how software can consolidate and contextualize past, present, and future operating risks and performance data for the enterprise across multiple sites and geographies, down to the asset.
Safety and profitability, previously diametrically opposed concepts, are needed in industrial plants and how. By leveraging an IIoT-enabled system architecture and safety applications, end users can create a closed-loop safety model to monitor any gaps between the design and performance of operations.
Stogner noted that everyone says safety is number one, but investments often don’t match that claim.
Safety is complex with many potential challenges. You only have to get it wrong once, Stogner said, to have a catastrophic experience.
Challenges helping shape software include simpler licensing, cybersecurity risks, business pressures, new regulations, fewer resources, more retirements, and less tribal knowledge.
Hendi said it’s useful to see plants or sites on a map and be able to drill down and see prediction layers in a risk matrix with a simple view of what’s happening. High-speed data collectors should bring data to one database that’s then connected to a distributed control system. Seeing the difference between design and what’s running in plant at any time helps accuracy.
Cloud visibility will help users understand what’s going on across the enterprise and allow a user’s expertise and collaboration to see a single source of truth to run operations safely and profitably, Hendi said.
Such solutions, Hendi said, should reduce the time of investigation in a refinery application by 30%.
Mark T. Hoske is content manager, Control Engineering, CFE Media, [email protected].
KEYWORDS: Optimization, automation
ARC Forum 2019 included manufacturing and process trends.
Optimization of production is among the key trends impacting manufacturing and automation.
CONSIDER THIS
Are you integrating new designs and technologies quickly enough to accelerate faster than your competitors?