New modular I/O technologies increase your options for communication with field instrumentation and devices. These are particularly useful when longer distances are involved.
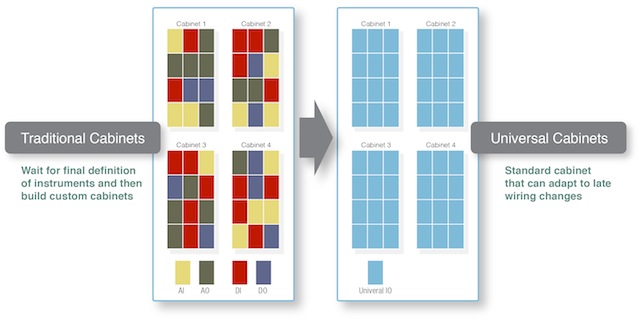
Advanced functionality with an easier setup: Creating a product that can be described with that phrase is the Holy Grail for just about every type of technology-dependent industry these days, and the increased demand for faster project completion and plant start-up have made it a necessity in manufacturing. The digital plant that seemed so futuristic just a few years ago is providing operators with functionality that most manufacturers never had before. There are still many strides that need to be taken, however, before faster and easier project completion—and therefore faster plant start-up—becomes normal.
One of the more recent advancements that stands to make significant inroads toward solving this problem is in the area of marshalling cabinets for field wiring, which for years have been used to connect signals from thousands of field devices to a control system in a logical and reliable way. This practice is very effective at grouping signals together according to I/O type, but it can be time consuming. Project schedules, however, are continuously being compressed, leading users to search for alternative methods of connecting the field signals to the control system.
Mounting I/O remotely in the field is one application that has particularly driven changes in marshalling practices. One such change is the concept of universal channel technology and universal cabinets that eliminate the need for marshalling by allowing any signal type, analog or digital, input or output, to be landed on any terminal and configured through software.
At first glance, this emerging approach appears to earn the elusive advanced-but-simple award, as simplifying field-to-control-room architecture can shave weeks and even months off project schedules while still delivering the advanced functionalities in high demand today.
Marshalling concepts
The approach for connecting field signals to process controllers follows a common formula: the field signal wiring is first brought to local junction boxes, which are then consolidated into more centralized junction boxes, which are then grouped into multi-core cables, often with common characteristics like low or high voltage, or analog or discrete. These multi-core cables are then brought into marshalling cabinets, where a variety of methods are used to connect the output of the marshalling cabinet to the control system. The goal of this philosophy is to bring all of the instruments into the control system in an orderly, maintainable, and robust manner that is still cost-effective from an installation and lifecycle standpoint. Three common methodologies for marshalling are half-knit, fan-out, and cross-wire.
Half-knit
Half-knit marshalling performs the scrambling on the system side. The field cables are terminated on marshalling blocks in pair order, making this very efficient and easy to maintain. This type of marshalling arrangement is suitable in several situations:
- Where cross-wiring is done in a remote instrument enclosure (RIE) or on site. In this case, the scrambling done between the marshalling blocks and I/O terminals is completely contained within the RIE.
- Where marshalling and I/O terminals are in the same system cabinet. Like the RIE example above, the scrambling done between the marshalling blocks and I/O terminals is completely contained within the cabinet.
- Where marshalling and I/O terminals are in different system cabinets, but the cabinets are permanently joined together.
It is less suitable when the marshalling and I/O terminals are in separate cabinets that are assembled in different places, or must be connected to conduct a FAT (factory acceptance test), then disassembled and reconnected when shipped to site. Once delivered on site, the connections between the marshalling and I/O terminals must be redone.
Fan-out
Fan-out marshalling is appropriate for systems where marshalling cabinets and system cabinets are connected during system staging and FAT, but need to be disconnected and shipped separately. The shipping dates may be different depending on construction schedule; often, marshalling cabinets are required several months earlier than system cabinets.
In this arrangement, field wiring is not terminated in pair order, and a custom termination is required per cable. Any spare pairs are left in the duct, increasing the risk of using those spare cores later in the operational lifecycle of the plant.
After FAT, the cables are disconnected from the system cabinets and coiled up in the bottom of the marshalling cabinets. On site, the cables are connected back to the system cabinets. Care must be given to the connectors, which can be damaged in a construction environment. The cable length must also be known during manufacture, which is much earlier in the process.
Cross-wire
From a high level, cross-wire marshalling combines elements of the half-knit and fan-out marshalling schemes. Cross-wire marshalling takes field cables and terminates them in pair order. Scrambling is done to the disconnects, fuses, or termination assemblies. Common prefabricated cables are used between the disconnects and system cabinets.
This solution is suitable when using separate marshalling and system cabinets. As different cable lengths are available with the prefabricated cables, the final room layout does not need to be known until much later in the process. Additionally, fuses, relays, or isolators can be installed between the field signals and the I/O terminals.
This marshalling scheme has the advantage of being easier to maintain, and it reduces the total amount of installation time on site since it is just a matter of plugging in prefabricated cables on either end of the solution. It has the obvious drawback of requiring additional cabinet space.
Comparison
Each of the three traditional types of marshalling has distinct advantages and disadvantages. The half-knit approach is useful in brownfield projects or where RIEs are used. It is also useful in situations where marshalling is done on one side of a cabinet and the I/O terminals are on the other side. However, if using separate marshalling and system cabinets and conducting FAT offsite, half-knit marshalling is a less attractive option.
Fan-out marshalling is useful when system cables or separate marshalling and system cabinets are specified, when marshalling cabinets are required on site well in advance of system cabinets, or the exact field cable details are not known during the design. This type of marshalling is more flexible and reduces the on-site construction schedule compared to half-knit, but is more challenging from an overall lifecycle perspective.
Cross-wire marshalling offers more flexible scheduling, delivery, and FAT options, while reducing schedule risk. It also comes with better lifecycle benefits than half-knit or fan-out marshalling. This does come with an increased initial cost, though.
Remote I/O with universal channel technology
As noted earlier, all the marshalling paradigms above share the same end goal: Connect field devices to the control system. They all start with the same basic assumptions: Instrumentation is located in the field, with field wiring being collected at junction boxes, which are brought into the marshalling cabinets, with home run cables connected to cabinets of I/O modules at some central location. The only real difference here is how the multi-core cables are treated in the marshalling cabinets and how they are connected to the control system.
More modern remote I/O practices challenge the assumption or requirement that I/O modules are kept in some central location. Moving I/O modules out into the field and closer to process instruments can eliminate the need for multi-core cables and marshalling cabinets, greatly simplifying the field-to-control room architecture. There are several benefits in using this remote I/O approach, which include reducing cost, improving the overall project schedule, and minimizing risk:
- Configurable channel remote I/O can reduce or eliminate marshalling. Since field signals can be landed directly on I/O terminals, the need for marshalling is eliminated. This has many benefits, including reductions in material costs, such as cabinets, conduits, home run cables, cable trays, and supports. It also reduces installed weight (important in floating production facilities), project labor costs, commissioning costs, and documentation costs.
- The overall system footprint in the central control room is reduced because the I/O is located directly at the process. The only cable runs to the central control room are now the I/O communication cables.
- Overall system flexibility is increased as spare channels are better utilized with more local options to I/O instead of being forced to wire back to a centralized location.
- Fast-track projects are easier to accommodate as the system can be tested and shipped prior to completion of field designs.
- Project execution efficiency is increased by standardizing supply chain requirements.
Many of these same benefits also apply to configurable universal channel technology, which allows for key modifications after control systems are commissioned and online. This approach drives on-site delivery schedules, since system engineering can be completed without impact from external design dependencies.
Configurable universal channel technology also liberates safety I/O, process I/O, and control cabinets from channel-type dependency. Universal I/O modules for both control and safety systems enable common design paradigms across an integrated control and safety system (ICSS). Any signal type can be connected to any channel without the need for additional hardware or interfacing modules. It also eliminates the need for custom hardware alignment with different I/O types. Cabinets can now be standardized, since any standard field signal can be connected to any I/O channel.
Because this approach can accept any signal type (analog, digital, input, or output), late arriving changes in the instrumentation package, as is commonplace in automation projects, can be accommodated through software configuration versus having to change the hardware. With universal I/O for both safety and process, project teams need only worry about I/O count and not the mixture of device types.
The configurable channel approach can not only reduce or even eliminate the need for marshalling but, most importantly, also allows immediate remote configuration. Theoretically, this would simplify engineering and configuration during the design stage of a project, and can save up to 33% of the installation costs. Late configuration changes can be done through remote access rather than having someone manipulating hardware in the field, so they can be handled in minutes rather than days.
Build in your shop, not the field
It is not difficult to imagine that cabinet requirements are also simplified by this approach. Often, the documentation required for design and fabrication of cabinets is not finalized in time to meet construction schedules on projects. This means that a lot of the cabinet assembly, testing, and configuration is done in the field, where costs are higher and efficient documentation is more difficult.
Universal cabinets are simply standard cabinets that are equipped with a configurable input capability. The resulting flexibility supports easy changes, additions, and modifications at any time without rewiring. The effort needed to obtain additional cabinets is minimized because the capabilities and resources of each cabinet can be determined in advance. Since there are no marshalling cabinets, the project ends up with an overall decreased footprint with lower installation and maintenance costs. Acceptance test schedules also are improved due to efficiencies in addressing late changes in I/O configuration. There are numerous other potential benefits:
- Universal cabinets can improve the project schedule by reducing the amount of custom engineering and documentation compared to custom designing each cabinet. Having universal cabinets enables a faster delivery that is based only on I/O count, not I/O type distribution.
- In addition to improved project schedules, universal cabinets can enable even faster and more cost-effective checkout.
- Adding room for spare devices is much simpler. Since every I/O channel can be configured as any point type through software configuration only, it is simple to adapt to late wiring changes. Instead of allocating I/O modules of each point type, which may or may not be used, configurable I/O modules are available for multiple point types.
- The total amount of I/O hardware is reduced. Here are two examples demonstrating a reduction in hardware needs. On a project with 5,000 I/O points, the total number of modules can be cut by as much as 35%. Even a small project can benefit since adding even one device with a different signal type requires adding a new module using traditional methods.
- For plants where instrument locations are highly distributed, such as a refinery tank farm, universal I/O modules in universal cabinets can be a very cost-effective alternative to long cable runs or additional RIEs.
Configurable channel technology is also useful in system migrations, especially in space constrained control rooms. Universal I/O modules can result in a negative footprint solution, and the module flexibility gives it the ability to adapt to existing field wiring with scalability to add new signals.
Even without mounting universal I/O modules remotely in the field, there are still other benefits. Universal I/O modules can be used in RIEs and equipment rooms to reduce or eliminate the cross-wiring requirements associated with the marshalling strategies discussed earlier.
These new I/O module approaches are particularly well suited for scenarios where the process is highly distributed or is modular. It’s important to remember, though, that each situation is unique, and different plants will have to weigh the benefits and costs of implementing each method. At the very least, these new I/O technologies have widened the number of available options for solving problems that demand advanced functionality with less complex installation. And that’s a major advancement in itself.
Joe Bastone is solution manager, Experion control and I/O, for Honeywell Process Solutions.
Key concepts:
- Traditional strategies for field wiring are proven, but can be costly and time consuming.
- New types of modular I/O devices support moving that connection into the field, closer to the devices.
- Software configurability of modules and individual channels allows for simpler hardware selection.
Go online:
For more information, visit:
www.honeywellprocess.com
Read more on I/O strategy below: