An integration project required upgrading legacy equipment in a tunnel that sees thousands of vehicles driving through every day without causing potential safety issues.
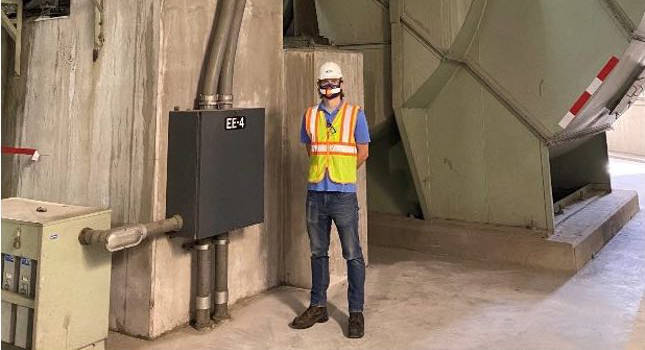
Learning Objectives
- The ventilation buildings for a pair of tunnels in Colorado needed a massive upgrade to their control systems, which hadn’t received any major upgrades since the 1970s.
- Variable frequency drives (VFDs), human-machine interface (HMIs) and motor control centers (MCCs) were among the equipment that needed to be upgraded.
- After the new equipment was installed, the legacy equipment was pulled out of service.
Among the highest-profile assets the Colorado Department of Transportation (CDOT) has are the Eisenhower – Johnson Memorial Tunnels. They usher millions of people either to or from a mountain ski getaway or across the country every year. At a capacity of up to 50,000 cars a day passing through, the reliability of vehicles and their drivers becomes a central issue – especially in the case of an accident.
The Eisenhower Tunnel (running East to West) and the Johnson Tunnel (running West to East) are required to be constantly equipped with a ventilation system that can evacuate smoke from the tunnels within 180 seconds. Removing the smoke through their ventilation system allows emergency vehicles to then enter the tunnels and push out the affected vehicle bringing safety to the many people hoping to continue their journey.
Project background
The tunnels, which were built in the early 1970’s, had seen some revisions over the years, but largely utilized many components from the initial builds. Through the control center, CDOT monitors the carbon monoxide levels in the tunnel and runs air in and out to prevent a toxic environment. The fans are also a means to suppress fire if there is a fire in the tunnel. CDOT needs to be able to control and monitor the fans from their control station to make the tunnel safer.
The engineering team was tasked with integrating replacement motor control centers (MCCs), new variable frequency drives (VFDs), programmable logic controllers (PLCs) and human-machine interfaces (HMIs) in each ventilation building electrical room and control room. There are 16 fans within the tunnels – both supply to push through the air and exhaust to suck out the air. The exhaust fans vent through the roof as seen in this picture.
From general contractors to electrical engineers and suppliers, this massive job took hundreds of hours and overcame some challenging initial issues.
Value engineering (VE) ideas
CDOT, as do other departments of transportation around the country, subscribes to a model of value engineering ideas, drawing on the expertise of engineers to find ways of maintaining or enhancing results while reducing lifecycle costs. The model, in existence since WWII, strives to engineer with an eye toward efficiency, expediency and cost-effective solutions. As a result, the engineers were able to apply the principles of value engineering based on CDOT’s requests.
Communication is key
All great business relationships are built on mutual trust and the engineering team was able to build relationships with everyone from the contractors and leads at CDOT, to the electrical contractor, the vendors and the operators to ensure a successful project. In the end, ensuring CDOT would be getting what they needed, wanted and could effectively use to operate safely and efficiently was the task at hand, as with all projects.
Communication in a multi-disciplined project depends on solid communication. From the big picture programming and equipment needs to the details of the customer meetings, it all required coordination between multiple parties.
Safety components
In addition to monitoring CO2 levels and any accidents or overheating vehicles that might travel through the tunnel, the engineers worked as a multi-faceted team. As the project progressed a decision to go with a manual shut-down model was made. This would ensure the safety of the employees working within the tunnel in the event of an emergency. This key recognition came through vital communication with the operators in the tunnels and their institutional knowledge of the safest model to use based on the personnel in the tunnel. As often happens with projects utilizing legacy equipment, when component parts malfunctioned, the engineers provided guidance to onsite operators and technicians to ensure the situation was mitigated and had a solution to fix the problem.
Updating legacy equipment
This project required extensive design and programming capabilities from an experienced engineering team and process improvements to the aging infrastructure. With little original documentation to base design off and old-fashioned light boards in operation, our team went to work on supervisory control and data acquisition (SCADA) screens and processes. Engineers constructed 40 local control stations (16 damper control station, 16 fan control stations and 8 cooling fan control stations) and 4 remote input/output (I/O) panels that contained RTD modules to monitor fan motor windings and digital input and output modules. VFD’s were programmed to enable the fans to run at incremental speeds lowering CO2 levels and providing more efficiency and power savings.
The equipment furnished under this specification replaced existing line-ups of motor control centers that were installed in the late 1970s. New equipment was installed in locations nearby the existing equipment, so the existing equipment remains in service. After the new equipment was installed, the engineering added SCADA screens with monitoring and control capabilities to existing switchgear. After normal operations were resumed using the MCCs and switchboards, the existing MCC lineup was taken out of service.
Averting a potential shutdown
Colorado has experienced shutdowns before due to weather related issues including avalanche warnings and mud slides. Though those shutdowns were unrelated to the tunnels, everyone involved knew the stakes were high to ensure this vital roadway remained open to travelers crossing the country. The idea of cutting off one of the main gateways from East to West due to ventilation issues was not acceptable.
Results
As an ongoing project with multiple phases, the relationship with CDOT has just begun as the engineering team begins the process of upgrading the Eisenhower Tunnel through the next series of upgrades.
Nick Hein is mechanical engineer; Sean Creager is senior electrical engineer, both at Huffman Engineering, a CSIA Certified Member; CSIA is a CFE Media and Technology content partner. Edited by Chris Vavra, web content manager, [email protected], CFE Media and Technology.
MORE ANSWERS
Keywords: worker safety, tunnel safety
ONLINE
See additional system integration stories at https://www.controleng.com/system-integration/
CONSIDER THIS
Have you worked on a project where equipment had to be removed while still safely serving customers?