ProfinetĀ is an open Industrial Ethernet solution designed to exchange data between controllers and devices in an automation setting.
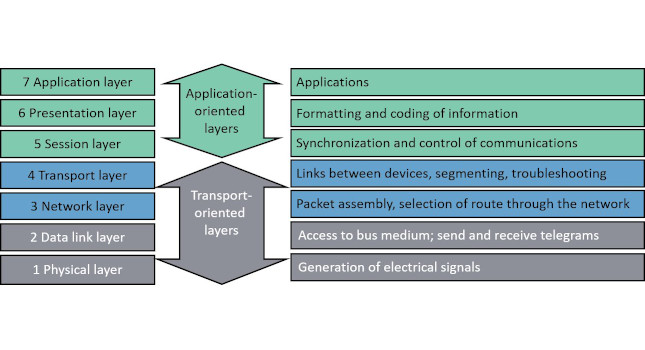
ProfinetĀ is an open Industrial Ethernet solution based on international standards. It is a communication protocol designed to exchange data between controllers and devices in an automation setting. It was introduced in the early 2000s and is the most well-adopted Industrial Ethernet solution.
Since Profinet is an open standard, hundreds of manufacturers have developed Profinet products.
Profinet defines cyclic and acyclic communication between components, including diagnostics, functional safety, alarms, and additional information. To link all of those components, Profinet employs standard Ethernet for its communication medium. Ethernet cables connect Profinet components within a network, allowing other Ethernet protocols to coexist within the same infrastructure. Besides Profinet, you can employ other Ethernet-based protocols to complement the network.
How Profinet works in industrial automation
Industrial automation environments often require high-speeds and deterministic communication. Deterministic communication means delivering messages exactly when they are expected.
Profinet must ensure messages are delivered with the appropriate speed and determinism depending on the task. Not all applications require the same performance. For example, loading configuration data for a process instrument can take several minutes without affecting production. On the other hand, a communication delay of just a few milliseconds between a programmable logic controller (PLC) and a high-speed variable frequency drive (VFD) can significantly impact the process.
To ensure appropriate performance, Profinet delivers data through the following communication channels:
- TCP/IP (or UDP/IP)
- Profinet real-time (RT)
- Profinet isochronous real-time (IRT)
- Time-sensitive networking (TSN)
Profinet can employ TCP/IP or UDP/IP communication for non-time-critical tasks, such as configuration and parameterization.Ā Due to the added latency and jitter associated with IP-based communication, this method is unsuitable for time-critical tasks.
Profinet employs a real-time channel to deliver data in a fast and deterministic fashion for time-critical applications.
This is how Profinet real-time works: Standard Ethernet frames have a field called an EtherType, which indicates the type of protocol used. Profinet real-time communication is set to have an EtherType of 0Ć8892. Upon arrival at the destination node, the frame is directed to the Profinet application immediately. The data goes directly from Ethernet, Layer 2, to Profinet, Layer 7. It skips the TCP/IP layers and avoids the variable time it could take to be processed as such. Thus, communication speed and determinism improve significantly.
Profinet real-time fulfills the requirements of the vast majority of time-critical applications. The overall performance will depend on your networkās design, but generally, you can achieve cycle times ofĀ 250 µs to 512 ms.
You do not need special hardware or configuration to use the Profinet real-time mechanism as all Profinet products are equipped with this capability.
Profinet IRT eliminates variable data delays by enhancing the rules used to switch Ethernet traffic and creating special rules for Profinet traffic. It fulfills all synchronization requirements and allows deterministic communication with cycle times down to 31.25 µs and up to 1 µs of expected delays, also known as jitter. Profinet IRT is optional and only required in specific high-performance applications, such as packing machines and printing presses.
This article originally appeared onĀ PI North Americaās website. PI North America is a CFE Media content partner. Edited by Chris Vavra, web content manager, Control Engineering, CFE Media, [email protected].