How do manufacturers get from automation to autonomy in industrial operations? Exploring the role of AI, digital twins and IT/OT convergence in driving efficiency, sustainability and innovation.
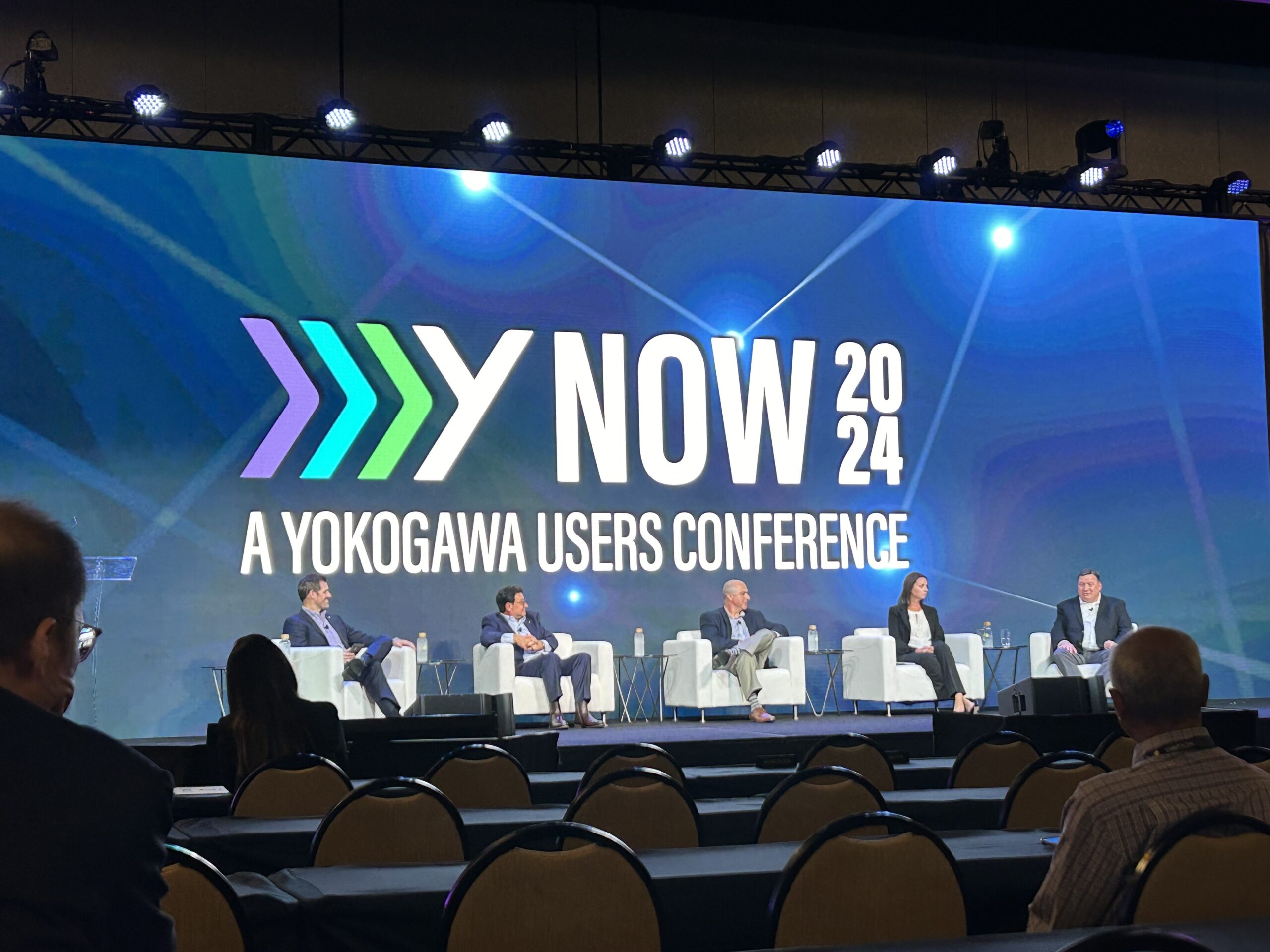
Process automation insights
- AI, digital twins and robotics are transforming process automation, enabling autonomy, predictive analytics and improved reliability.
- Integrating operational and information technology enhances collaboration, centralizes operations and supports predictive maintenance.
- Automation drives green energy projects, while open standards ensure interoperability and future-ready systems.
Process automation continues to evolve with the integration of advanced technologies such as artificial intelligence (AI), digital twins and robotics. This dynamic transformation holds significant implications for distributed control systems (DCSes) and their applications in modern industries. These innovations are increasing operational efficiency, while paving the way for sustainable solutions and more resilient industrial processes.
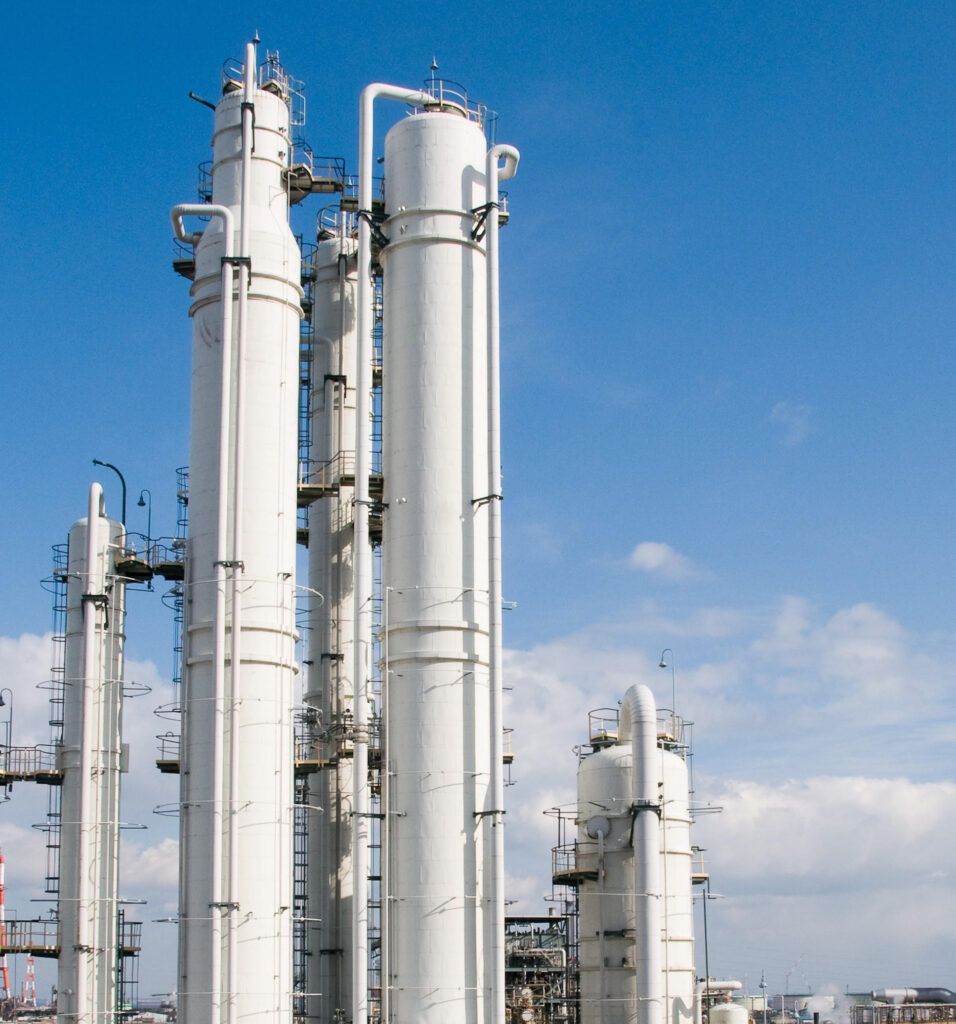
Advanced technologies redefining process automation
Recent strides in AI have enabled autonomous control of intricate systems, such as distillation columns, in chemical plants. Reinforcement learning algorithms like factorial kernel dynamic policy programming (FKDPP) showcase the potential to create self-learning systems. These algorithms allow plants to achieve advanced control strategies that were previously unattainable, enhancing performance and reliability in complex operations.
Mitsuhiro Yamamoto, vice president and executive officer of the Systems Business Division, Digital Solutions Headquarters, Yokogawa Electric Corporation, noted, “With regard to the realization of autonomy through AI, an important milestone is autonomous control using FKDPP. This algorithm learns by itself in simulations, and then generates highly robust control models that cannot be achieved with conventional control models to achieve advanced control. Beyond that, we believe that generative AI will open up new possibilities in plant operations. Yokogawa will support digital transformation in the OT [operational technology] domain by providing data analysis, abnormality prediction and decision support to operators using generative AI.”
Digital twins are expanding the scope of process automation by creating virtual models that provide predictive analytics and enhanced measurement capabilities. Engineers can utilize these models to anticipate issues and optimize performance. These virtual representations of physical systems enable better planning and simulation, leading to significant cost savings and reduced downtime.
“We believe that advances in digital twin technology are an enabler of autonomous operations,” Yamamoto explained. “The digital twin will make it possible to measure things that cannot be measured in reality, and to predict the future, expanding the scope of the twin, which in turn will broaden the scope of its application for autonomous operations.”
The integration of robotics with the DCS is another critical advancement. Robots not only conduct site inspections, they can also respond to alarms, feeding real-time data into control systems. This enhances situational awareness and allows for immediate corrective actions.
“With regard to robotics, Yokogawa has realized the integration of DCS and robots through the Robot Management Core, which provides a single-user interface for different robots from multiple suppliers,” Yamamoto said. “We envision a future where DCSes and robots work together. For example, the alarm triggered by the DCS can be used to trigger the robot to inspect the site and address the problem. Also, data collected by the robot during its rounds of inspection can be reflected in DCS operations in real time.”
IT/OT convergence is helping fuel digital transformation
IT/OT convergence bridges operational technology with information technology (IT) to unify plant operations with enterprise systems. This integration facilitates efficient collaboration and operational transparency, unlocking innovative opportunities for process management. By breaking down traditional silos, IT/OT convergence fosters a holistic approach to operational excellence.
Key platforms for IT/OT convergence ensure secure handling of OT data, while enabling comprehensive analysis and collaboration. Yokogawa was recently selected as main automation contractor for Shell’s Holland Hydrogen I project, and it is providing the integrated control system and the energy management system for the Yuri Green Hydrogen project in Australia. The company also provided a remote operation/monitoring system and a video monitoring solution for the Ishikari Bay New Port Offshore Wind Farm, the largest wind farm in Japan. All of these projects utilize Collaborative Information Server (CI Server).
“We position CI Server as a core product for implementing IT/OT convergence, and we want to promote the use of IT and OT data while keeping plant operations secure, and providing new applications and additional customer value through co-creation,” Yamamoto said.
Centralized operations management is a practical application of IT/OT convergence. Multi-site factories can benefit from consolidated monitoring and decision-making capabilities, improving coordination and operational insight.
“One Japanese customer has several factories and wants to integrate the operations of all these factories, so they are using the CI Server because it will connect to the outside world,” Yamamoto said. “An operations expert can be in one place and have an eye on all factories. It can also be used to create something like an integrated operations center not only for Japan, but also for overseas.”
This convergence also facilitates advanced analytics and machine learning applications, providing operators with actionable insights. This capability is vital for predictive maintenance, energy optimization and real-time decision-making — ensuring that plants remain competitive in a rapidly changing industrial landscape.
Sustainable innovations in process automation
Automation technologies are increasingly critical to support sustainable projects, such as green hydrogen production and renewable energy storage. Recent projects, including offshore hydrogen platforms integrated with automation systems, highlight the role of advanced solutions in achieving environmental goals.
Yokogawa Italia recently received an order to supply an integrated automation and energy control and monitoring system for the Baseload Power Hub, a pioneering offshore green hydrogen production and storage pilot plant within a wind farm developed by CrossWind, a joint venture between Shell and Eneco. CI Server will play an important role in this complex system.
“CI Server provides the following functions required for IT/OT convergence. It ensures security for OT data and does not affect safe and secure plant operations; collects a wide variety of scattered OT data and enables wide-ranging collaboration; understands the interrelationships and meanings of IT and OT data; and builds a normalized information model,” Yamamoto said.
These sustainable solutions align with global efforts to reduce carbon emissions and promote renewable energy adoption. Automation systems are critical for managing the complexities of these projects, ensuring efficiency and scalability.
For example, automation enables precise control and monitoring of energy flows in green hydrogen plants, optimizing production processes and minimizing waste. These systems also provide robust data analytics, allowing stakeholders to evaluate the performance and environmental impact of their operations in real time.
Open process automation: flexibility and interoperability
Open process automation (OPA) standards are transforming process automation by enabling interoperability across diverse components. These systems provide engineers with scalable solutions that integrate legacy infrastructure with modern technologies. OPA ensures that organizations can adopt new technologies without discarding existing investments, creating a cost-effective path to modernization.
“OPA aims to achieve the interoperability and portability of systems by standardizing communication methods and information models through the use of standard specifications,” Yamamoto explained. “It provides process manufacturers with further optimization of their plant operation management. The Open Process Automation Standard (O-PAS) and the application of open technologies in process automation are still in their early stages, but progress is being made. Yokogawa will support Open Process Automation Forum (OPAF) to evolve the O-PAS and build out the certification program, and help the industry adopt OPA by participating in OPAF and serving as an OPA system integrator, service provider and component supplier.”
By fostering interoperability, OPA reduces vendor lock-in and encourages innovation. Engineers can now build systems that are adaptable to future technological advancements, ensuring long-term sustainability and competitiveness.
From automation to autonomy: the next frontier
At an October event in Houston, Yokogawa discussed the shift from automation to autonomy in industrial automation. Moving toward autonomy represents a transformative leap in process control, where autonomous systems leverage AI, digital twins and robotics to perform self-directed operations, requiring minimal human intervention. This evolution marks a paradigm shift, as industries move toward systems capable of making independent decisions based on real-time data and predictive analytics.
“Our business is centered on the DCS, and we would like to innovate the DCS by using the power of DX [digital transformation],” Yamamoto said. “Automation and autonomy are very different. The CI Server is a key for enabling autonomy and the system of systems concept.”
Autonomous systems are designed to operate under varying conditions, adapting to changes without manual input. This capability is particularly valuable in industries like oil and gas, where operational environments are often unpredictable. By reducing dependency on human operators, these systems improve safety, reliability and efficiency.
Moreover, autonomous systems facilitate the creation of smart plants that can optimize operations continuously. These plants are equipped with sensors and analytics tools that provide a comprehensive view of operations, enabling real-time adjustments and long-term planning.
Redefining process automation
The integration of advanced technologies is redefining process automation. Engineers must stay abreast of these trends to drive innovation and meet the demands of evolving industries. By embracing tools like AI, digital twins and robotics, engineers can contribute to the transition from automation to autonomy, fostering progress in process automation.
The convergence of IT and OT, advancements in AI and the adoption of OPA standards are setting the stage for a new era in industrial operations. As the industry progresses, these technologies will play an instrumental role in achieving operational excellence, sustainability and resilience.
KEYWORDS
Process automation, digital transformation, sustainability
LEARNING OBJECTIVES
- Learn how AI, digital twins and robotics are enabling autonomy, improving operational efficiency and enhancing industrial reliability.
- Gain insights into how integrating operational and information technologies drives digital transformation, centralized operations and real-time decision-making.
- Discover how automation technologies support green energy projects and ensure flexibility through open process automation standards.
CONSIDER THIS
How can the integration of AI, digital twins and robotics in process automation accelerate the transition from traditional automation to full autonomy in industrial operations?